When the electric furnace taps steel, the furnace body tilts to a certain angle (usually 45°) in the tapping direction. The molten steel flows through the tapping trough and enters the ladle. In addition to guiding the molten steel, the tapping trough also prevents the molten steel from scattering. , protect molten steel and reduce secondary oxidation. If the geometric shape design or the use of refractory materials is improper, it will lead to large heat loss, high refractory material consumption, and even increase non-metallic inclusions in the molten steel.
The structure of trough tapping is that the tapping port is located above the water surface of the steel. In the past, the tapping method of the tapping trough was to tap the molten steel with steel slag covering it. The main purpose was to prevent the temperature drop of the molten steel, improve the desulfurization capacity, and prevent the oxidation of the molten steel. . Now the tap hole starts from close to the furnace bottom, and is connected to the large upward-sloping tap trough at the outer flat wall. The cross-section of the tap hole and the tap trough is as shown in the figure.
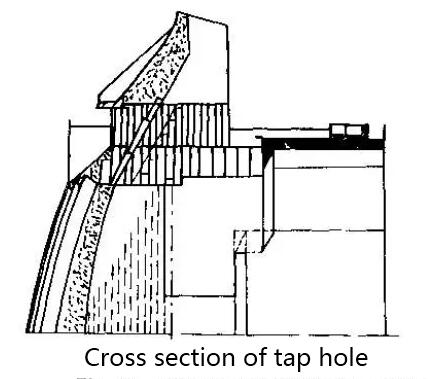
The tapping trough is connected to the furnace shell, and its masonry methods include pounding, pouring, brick masonry or comprehensive masonry. The masonry method of the taphole is relatively consistent. Generally, taphole bricks of various shapes are used to build the taphole or the center is a steel pipe, surrounded by high-quality magnesium oxide castables. Ceramic pipes with a wall thickness of 25mm and 2 to 3 pieces are also used. Made of high-grade fused magnesia bricks. Usually after 50 to 70 furnaces are used, a new tap hole needs to be replaced. When the tapping trough is tilted to tap steel, the main damaged parts are the molten steel line, the slag line, and the bell mouth at the front end of the trough. The refractory materials are required to have good wear resistance, slag corrosion resistance, and thermal shock resistance, and must be used during the use of the tapping trough. Prevent cracking and minimize wear and tear.
The material of foreign electric furnace tapping trough is generally made of high aluminum, magnesium aluminum, zirconium, magnesium carbon, wax stone, etc. or SiC, Si3N4 and C and oxidants are added and the service life can reach more than 100 times after maintenance and repair. of more than 300 times.
A brick-built steel channel
Japan uses highly durable CFC-ZRN-15X zirconium bricks, which are made of pure zircon as the main raw material, supplemented by silicon nitride that is resistant to molten steel erosion, making them excellent in adhesion and erosion of molten steel and erosion of molten slag. It has anti-corrosion effect, but it is more expensive. This brick is built in a 50t electric furnace and a 1.95m long tapping trough. It has a service life of 300 furnaces for smelting ordinary steel. Used for 100t electric furnace, 2.8m long tapping trough, smelting special steel with a service life of 200 furnaces.
In addition, CFC-ZRN-15X semi-zircon bricks are also used. This brick uses pure zircon as the main raw material and uses some high-grade siliceous raw materials to give it the properties of semi-zircon bricks. The price is lower than that of pure zircon and silicon nitride. Brick is much lower. Used for 40t electric furnace, 0.9m long tapping trough, smelting ordinary steel with a service life of up to 300 furnaces.
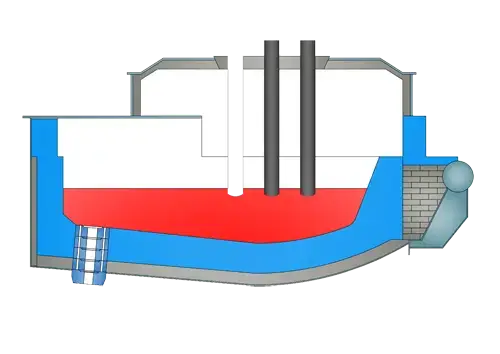
B prefabricated block tapping channel
The use of prefabricated large blocks to build the tap trough has minimal brick joints, which is beneficial to extending the life of the tap trough, while reducing construction time, and can be mechanically hoisted and can be used after installation. In the 1980s, prefabricated blocks of high-aluminum and low-cement castables were widely used in Japan to create steel troughs. The castable uses alumina as aggregate, silicon carbide and flake graphite as main raw materials, and adds special ultra-fine powder and dispersant.
The 80t electric furnace uses low-cement castables and aluminum-carbon prefabricated blocks to build a steel trough with a service life of 118 furnaces. The original resin-bonded ramming-shaped steel trough has a service life of only 20 to 40 times.
C integral tapping channel
The tapping trough is generally made of amorphous refractory materials, which have good integrity, long service life and low cost. The materials used include ramming materials using phenolic resin as a binder or vibrating castables using non-cement systems as a binder, which can generally be prepared and constructed on site.
D Comprehensive masonry tapping channel
Japan’s Osaka Kiln Refractory Brick Company switched to using high-pressure pressed Al2O3-C unburned bricks to build the main part of the tap trough, and the end of the tap trough still uses the original Al2O3-SiO2-C-SiC ramming structure.
The use results show that the main part of the tap chute (made of Al2O3-C) has a service life of up to 6 weeks (613 furnace), and the service life of the end of the tap chute is about 2 weeks. The overall usage situation is that the melting loss rate of the Al2O3-C tapping trough is 1/6~1/7 of the original high-aluminum tapping trough.In addition, Japanese tap troughs also use MgO-C bricks. MgO-Cr2O3 bricks produced by Osaka Company are used in electric furnace tapping troughs due to their high high-temperature strength, good volume stability, corrosion resistance, and thermal shock resistance.
The French Lafarge company uses a pre-cast high-aluminum lining at the taphole of the electric furnace. The mouth of the tapping chute is opened as low as possible in the furnace. During the tapping process, the slag surface is kept above the tapping mouth so that the slag will not flow out when the furnace is tilted. The properties of RERCAST10 grade high aluminum castable are as follows: chemical composition (%) is Al2O376.3, SiO26.5, SiR4.8, C6.8; volume density is 3.05g/cm3; normal temperature compressive strength (MPa) is 1100℃ 75, 60 at 1200℃; the permanent line change rate (1200℃) is -0.3%. West Germany’s 100t electric furnace uses magnesia carbon bricks to build the tapping trough, with a service life of 100 to 150 times.
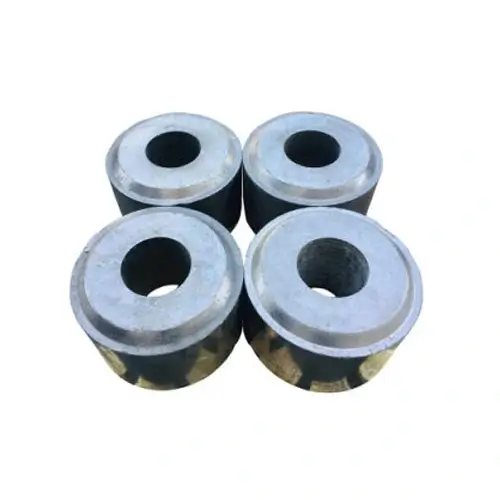
In China, tap troughs are generally built with high-aluminum, magnesia-aluminum, magnesia-carbon, etc. When the tap trough lining is built with small bricks, the brick joints are severely melted, and steel slag is easily seeped through, making it difficult to clean. In the 1970s, the application of bauxite cement tapping troughs in electric furnaces was comprehensively promoted. High-aluminum clinker was used as the aggregate and bauxite cement was used as the binding agent. The production process of mixing, trapping, vibration forming, curing, and natural drying was used to produce the steel. groove. The service life of this bauxite cement integrally formed tapping channel is about 80 to 100 times for electric furnaces below 3t, and about 20 to 30 times for electric furnaces above 5t. The high aluminum rammed or vibrated integral tapping trough that uses phosphoric acid instead of alumina cement as the binding agent has a short service life due to water absorption problems. The integral tapping trough uses water glass as the binding agent and steel fiber as the reinforcing material. Due to its poor corrosion resistance, its use effect is also poor. Later, integral tapping troughs with low-cement castables of different materials were developed. In order to improve the performance of aluminum-silicon castables, the following technical measures should be taken:
(1) Matrix composition. The composition of the matrix has an important influence on the service temperature, high-temperature mechanical properties and sintering properties of the castable. The matrix should be mainly bauxite clinker with low K2O and Na2O content. Control the amount of cement added and optimize the ingredients to make the matrix of the castable similar to the chemical composition of mullite. That is, the content of Al2O3 and Si02 in the matrix is adjusted so that it can generate mullite at high temperatures and produce micro-volume expansion to improve thermal shock resistance and high temperature strength.
(2) Binder. Use pure calcium aluminate cement as the binding agent. Its main components are CaO·Al2O3 (calcium aluminate, decomposition temperature 1600℃, high activity, normal coagulation speed, fast hardening speed, high early strength, and no obvious strength increase in the later period; CaO·2Al2O3 (calcium dialuminate, decomposition temperature 1762 ℃), the hydration and hardening speed is slow, the early strength is low, and the later strength is high. Through the hydration and coagulation of the cement, the aggregate and powder are cemented together, and the addition amount is less than 5%.
(3) Add appropriate amount of micro powder. The addition of micro powder can fill the gaps between particles, improve the internal structure, produce cohesion and bonding to densify it; at the same time, it can significantly improve fluidity and significantly reduce construction water consumption. At 110°C, if the addition amount is greater than 8% in 24 hours, the shrinkage of the castable will increase and there will be more cracks, so 4% to 5% is appropriate.
(4) Dispersant. Adding an appropriate amount of dispersant (water reducing agent) can improve the dispersion of fine powder particles in the castable, increase the distance between particles, reduce gravity and friction, further improve the fluidity of the castable, and at the same time discharge the free water surrounded by particle agglomerates , make the castable fluid and reduce its construction water consumption. If sodium tripolyphosphate is used as the dispersant, the appropriate addition amount is 0.05%~0.5%.
(5) Add expansion agent. Quartz, the high-temperature decomposition product of kyanite, reacts with (Al2O3) in the powder to form secondary mullite (3Al2O3·2SiO2). The volume micro-expansion can offset the shrinkage of the material to improve thermal shock resistance. 3Al2O3•2SiO2 can form a solid solution with Fe2O3 and TiO2 in the matrix, effectively reducing the amount of liquid phase at high temperatures to improve its high temperature performance. The amount added should be less than 10%
(6) High temperature enhancer. Corundum has the characteristics of high melting point, stable chemical properties, and good high-temperature strength. It is appropriate to use less than 0.088mm powder with an addition amount of less than 15%.
(7)Construction water consumption. After the castable is dried, the flexural strength of the product is inversely proportional to the amount of water added during construction, which is about 5%.
E compound tapping trough
The tapping trough consists of a working layer (magnesia carbon brick MgO ≥ 75%, C ≥ 15%, apparent porosity ≤ 6%, volume density ≥ 2.8g/cm3, normal temperature compressive strength > 32MPa) and a non-working layer (refractory castable )composition. The non-working layer is assembled from prefabricated blocks.
The composite tapping trough is used in a 5t electric furnace (actual tapping capacity is 18t), the tapping temperature is 1600~1650°C, 66 tapping troughs are used, the maximum use is 93 times, the average life is 80 times, and the average erosion speed is 1mm. The composite tap trough is made of reasonable materials and has low cost. It can reduce thermal shutdown time in synchronization with the age of the furnace and improve the operating rate. The life of the tap trough is 3 to 4 times longer than that of high-aluminum refractory castables. It adopts an assembled and lined integral body. The structure, storage and transportation are convenient to use.
Al2O3-SiC-C castable tapping trough is used for 5t (steel tapping capacity: 10t) electric furnace, with a service life of 121 times. The inner diameter of the tapping trough is 0.3m, the wall thickness is 0.2m, and the entire tapping trough uses 1.7t of castables. The bottom is permanently lined with bauxite cement refractory concrete (material used: 0.7t), and the upper working layer of the trough is made of Al203-SiC-C castable (material used: 1.0t). The tapping trough is non-stick, corrosion-resistant and resistant to slag. It washes away and the working surface becomes smooth after use. It is an ideal castable.
The castable is made of super high-grade bauxite clinker as the main raw material, with an appropriate amount of SiC (particle size <0.088mm accounting for 90%), carbonaceous materials (<0.1mm) and alumina powder, etc., and an appropriate amount of antioxidants, The sintering agent and dispersant use pure calcium aluminate cement as the binding agent. The chemical composition (%) of the castable is: Al2O363.67; SiCi2.05; SiO213.7; C7.61. Tianjin No. 3 Steelmaking Plant uses magnesia carbon bricks instead of brine magnesia ramming materials in the 5t electric furnace tapping trough. The average washout per furnace is 0.3~0.66mm. After use, the surface is smooth, which can reduce non-metallic inclusions in the steel and extend the tapping time. Service life of steel tank.
F low cement castable integral tapping trough
Chongqing Special Steel’s 10t electric furnace uses an integral tapping trough, with a smelting temperature as high as 1650~1750°C. No cracks or structural peeling occurred during use. The corrosion rate of the copper outlet is 1.8~2.4mm/furnace. The one-time service life without repair can reach more than 50 furnaces. The tapping trough adopts vibration molding to feed materials in batches, and is then demoulded after 24 hours of standing curing. After demoulding, it is naturally cured for more than 48 hours, and the final baking temperature reaches 600°C. This tapping trough attaches great importance to the production process. The properties of the three high-aluminum castables are shown in Table 2-69.