Although carbon-containing refractory materials have significant resistance to molten steel erosion, slag resistance, good thermal shock resistance and high temperature flexural strength, the oxidation problem of carbon limits its service life, and the magnesia carbon bricks are damaged during use. Mainly due to the oxidation of carbon by iron oxides in the slag and the reduction of MgO by carbon at high temperatures, a decarburization layer is formed, which leads to the deterioration of the organizational structure of magnesia-carbon bricks and promotes the erosion of the slag towards the decarburization layer. During the reaction The appearance of low-melting substances causes melting and erosion as well as the oxidation of carbon by oxygen in the furnace body. In aluminum carbonaceous refractory materials, in addition to the oxidation of carbon, the additive aluminum powder reacts with carbon (4Al+C=Al4C3 ) to generate aluminum carbide whiskers, but aluminum carbide is prone to hydration reactions when exposed to water, resulting in a large amount of volume expansion. Therefore, cracking and powdering often occur, which greatly shortens the service life and frequency of refractory materials.
1.Damage mechanism of alumina-magnesia carbon bricks
The damage forms of alumina-magnesia carbon bricks are mainly abnormal damage, chemical erosion of the refractory brick components caused by molten slag and molten steel; wear, thermal spalling and structural spalling caused by the flow of slag and molten steel; oxidation of carbon; chemical corrosion caused by the flow of slag and molten steel wear and tear.
A.Chemical attack
The common CaO-SiO2-Al2O3 series slag and FeO in the slag will react with the alumina and magnesia in the alumina-magnesia carbon bricks. In order to prevent alumina-magnesia carbon bricks from forming a solution on their own due to the inclusions in the brick composition and the Si compounds added to prevent oxidation, which promotes chemical corrosion with the slag, the SiO2 component should be reduced as much as possible, and fused magnesia should be used. Purity magnesia and high purity graphite.
B. Peeling off
The main damage forms of alumina-magnesia-carbon bricks are spalling and chemical erosion. The generation of spinel and the invasion of slag have a great impact on the spalling of alumina-magnesia-carbon bricks. After the alumina-magnesia carbon brick is heated, spinel will be generated between the magnesia and alumina. The generated spinel will expand the volume of the brick, causing micro-cracks in the matrix part, and the micro-cracks and gaps around the MgO particles are connected. As a result, the slag invades into the interior of the brick, causing the brick to be chemically attacked and structurally peeled off. In order to suppress this phenomenon, it is necessary to control the amount of spinel generated and the composition of the magnesia particle size in the alumina-magnesia carbon brick.
C. Oxidation of carbon
When resin-bonded alumina-magnesia carbon bricks are dried after construction, the carbon in the preheated bricks will undergo gas-phase oxidation with oxygen in the air, forming a decarburized layer that will promote chemical erosion and wear. This requires the formation of a slag layer on the working surface to isolate the air. At the same time, in order to improve the oxidation resistance, appropriate addition of antioxidant materials is required.
For alumina-magnesia carbon bricks, the mineral change of spinel generated during use has a great impact on the damage form, so the generation and quantity of spinel should be controlled.
2.Damage mechanism of magnesia carbon bricks
Due to the oxidation of carbon and the formation of a decarburization layer, coupled with the huge difference in thermal expansion rates of magnesium oxide and graphite at high temperatures (1.4% and 0.2% respectively at 1000°C), the structure of the material becomes loose, the strength is reduced, and after melting Due to the erosion of slag and mechanical erosion, the magnesium oxide particles in the bricks are gradually eroded and fall off layer by layer, causing damage to the magnesia carbon bricks. The damage process of magnesia carbon bricks is divided into the following steps: oxidation of carbon – formation of decarburization layer – loose structure – slag erosion – mechanical erosion – structure falling off – damage.
Above 1600°C, magnesium oxide reacts with carbon to generate a large amount of gas, which is the main cause of damage to magnesia-carbon bricks.

When the carbon in the working lining hot surface of the magnesia carbon brick is oxidized, a thin decarburization layer is formed. The formation of the decarburization layer is mainly due to the oxidation of the carbon by the iron oxides in the slag and O2 in the air as well as CO2, SiO2, etc. The result of material oxidation also includes the vaporization effect of MgO dissolved in molten steel or bricks on carbon; when high-temperature liquid slag penetrates into the pores in the decarburization layer or into cracks caused by thermal stress. , the molten slag will react with the oxidized cast in the bricks to form low-melting-point compounds. These low-melting-point compounds will cause qualitative changes on the surface of the bricks and cause them to fall off and be damaged layer by layer under the stress of strong agitation of the steel slag and mechanical erosion, and so on. , the furnace lining becomes thinner layer by layer, and eventually the furnace is repaired, repaired, and stopped.
A. Oxidation of carbon
It is precisely because carbon oxidation destroys the carbon network structure in the brick that the brick’s organizational structure is loose, the strength of the product is reduced, and the pores are correspondingly increased. At the same time, the erosion of the brick by the slag is intensified. The oxidation of carbon is mainly through the following reaction ongoing.
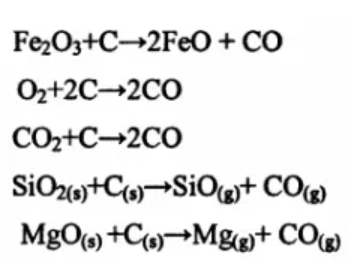
B. Influence of stomata
Another important factor affecting the damage of magnesia carbon bricks is the pores in the magnesia carbon bricks, especially the open pores. The pores provide a channel for the oxidation of carbon, and also intensify the erosion of the slag on the brick lining, thus causing damage to the magnesia carbon bricks. . On the one hand, when cooling, the open pores in the brick suck in air from the outside. When heating, the oxygen in the air reacts with the surrounding carbon to generate CO samples, and the cycle repeats, increasing the porosity. On the other hand, the binding agent in magnesia carbon bricks is an important factor in the generation of pores. As the binding agent of magnesia carbon bricks, phenolic resin is generally added in an amount of 3% to 4%. The porosity of the molded product is about 3%. During the use of the product, the phenolic resin is heated and decomposed to produce a large amount of H2O, H2, CH4, CO, CO2 and other gases that are evaporated and discharged, forming a large number of pores, allowing oxygen in the air and oxides in the slag to pass through. The pores corrode the bricks, which not only promotes the oxidation damage of carbon, but also intensifies the reaction between slag and MgO in the bricks, causing damage to the magnesia carbon bricks.
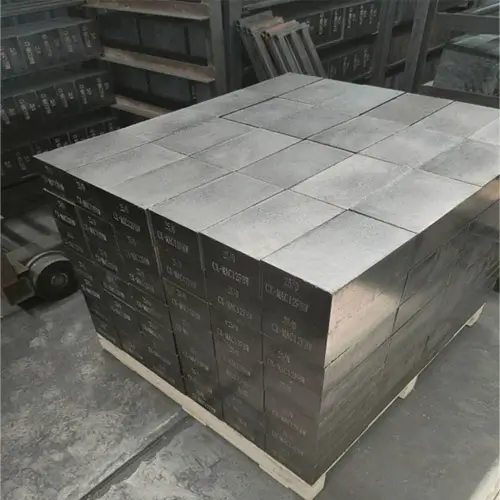