In recent years, some steel casting companies in our country have adopted spinel-type furnace lining materials. Among them, some manufacturers purchase materials pre-prepared by foreign manufacturers. Although the use effect is very good, the production cost has increased a lot, and its characteristics are not good. Very understanding. This article mainly wants to introduce some characteristics of spinel-type refractory furnace linings for reference when colleagues prepare their own furnace lining materials and further improve furnace lining materials.
(1) Silica sand furnace lining
Furnace linings made of silica sand as the basic refractory material are also commonly called acid furnace linings. Silica sand has many advantages: first, it is rich in resources and low in price; and crucibles made of silica sand as the basic refractory material still have good strength at high temperatures close to its melting point, and have good resistance to sudden cooling and sudden heating; In particular, it should be mentioned that during the sintering process of the furnace lining, the quartz phase change expansion of the silica sand can compensate for the volume shrinkage during the sintering process, thereby increasing the density of the sintered layer and reducing the porosity in the sintered layer of the furnace lining. Therefore, in the foundry industries of various countries, silica sand-based lining materials are widely used in crucible-type induction furnaces used to smelt various cast irons.
However, SiO2 has low refractoriness and basically cannot adapt to steelmaking temperatures. Moreover, SiO2 has strong chemical activity at high temperatures and can interact with various alkaline oxides and even neutral oxides in the steelmaking process. For example, when FeO comes into contact with silica sand, it is easy to generate fayalite with a melting point of 1205°C ( Fe2SiO4), fayalite can further interact with SiO2 or FeO to generate a eutectic component with a melting point of 1130°C. In addition, SiO2 may also be reduced by some more active elements in the molten steel. Therefore, when silica sand furnace lining is used for steelmaking, it can neither guarantee the metallurgical quality of the steel nor the life of the furnace lining. Since the late 1980s, foundries in various industrial countries that use induction furnaces to produce steel castings have no longer used silica sand furnace linings. As far as I know, some companies still use silica sand furnace linings to smelt cast steel. This situation needs to be improved urgently.
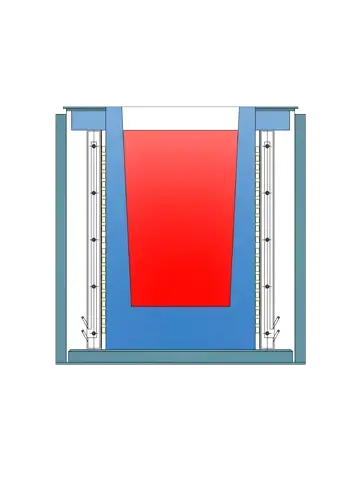
(2) Magnesia furnace lining
The commonly used furnace lining material is metallurgical magnesite with an MgO content of more than 86%, which is made from magnesite calcined at high temperature. If the metallurgical magnesia is remelted in an electric arc furnace, the content of SiO2, Fe2O3 and other impurities can be reduced, and fused magnesia with higher purity (MgO content above 96%) can be obtained. Fused magnesia is mostly used to make the lining of vacuum induction furnaces.
Metallurgical magnesia has a high refractoriness and is a conventional lining material for alkaline electric arc steelmaking furnaces. Although its melting point is very high, it is not easy to sinter, and its expansion coefficient is large. However, because the lining of the electric arc furnace is very thick, by adding a large amount of Bonding materials and wet knotting can completely make up for this shortcoming.
If metallurgical magnesia is used as the lining material of the induction furnace, due to the restriction of the thickness of the furnace lining and the inability to use wet knotting, the negative effects of these shortcomings will be very obvious. Crucibles made of magnesium oxide are prone to cracks, especially in furnaces that operate intermittently.
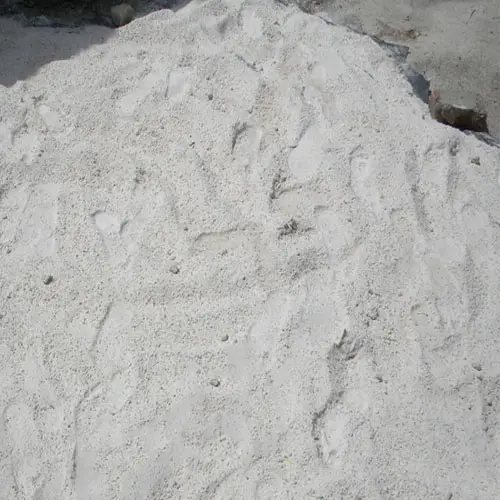
(3) Alumina furnace lining
Alumina and zircon sand are both neutral refractory materials. Among them, alumina is the most widely used, and zircon sand is rarely used as furnace lining material.
Using alumina alone as the furnace lining material has a strong ability to resist cracking and prevent acidic slag erosion, but it is not suitable for making alkaline slag. Moreover, due to its high refractoriness and poor sintering performance, the furnace lining life is not very high.
(4) Spinel type furnace lining
Spinel minerals have homogeneous characteristics, with many varieties and complex compositions. Its molecular formula can be written as M2+O·M3+2O3, where: M2+ represents some divalent metal atoms, such as Mg, Fe, Zn, Mn, etc.; M3+ Represents some trivalent metal atoms, such as Mg, Fe, Zn, etc. Therefore, it can also be written as (Mg,Fe,Zn,Mn)O•(Al,Cr,Fe)2O3.
Among the divalent metal atoms contained in spinel minerals, Mg2+ and Fe2+ can replace each other in any proportion; among the trivalent metal atoms contained in spinel minerals, Al3+ is the majority, but Cr3+ can replace Al3+ in any proportion, while Fe3+ can only replace Al3+ in a certain proportion. Replace Al3+ or Cr3+ within the limit. Common spinels include the following:
Magnesium aluminum spinel MgO·Al2O3
Aluminum spinel FeO·Al2O3
Chromite (iron-chromium spinel) FeO·Cr2O3
Magnetite (iron spinel) FeO·Fe2O3
Magnesia spinel (Mg,Fe)O•(Al,Fe)2O3
Zinc aluminum spinel ZnO·Al2O3
Magnesia Chromium Spinel MgO·Cr2O3
Zinc iron spinel ZnO·Fe2O3
Manganese chromium spinel FeO·Cr2O3
Manganese aluminum spinel MnO·Al2O3
At present, in various industrial countries, the main material used as the lining material of induction furnaces for steelmaking is magnesia-aluminum spinel (MgO·Al2O3), which is usually referred to as ‘spinel’. In pure magnesia-aluminum spinel, the MgO content is only 28.2%, but it is still an alkaline refractory material.
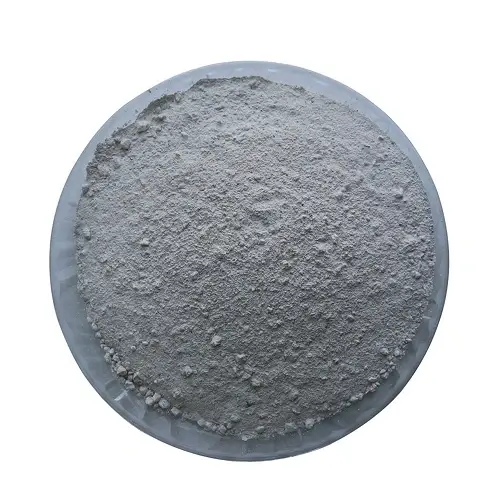
Magnesia-aluminum spinel-based materials have high refractoriness, small thermal expansion coefficient, good thermal stability at high temperatures, and strong resistance to alkaline slag erosion. In particular, it should be mentioned that MgO and Al2O3 have a volume expansion of 7.9% during the sintering process to form spinel, which can compensate for the volume shrinkage during the sintering process and reduce the porosity of the sintered layer. This is an important advantage of the silica sand furnace lining. are consistent.
Spinel type furnace lining materials are not actually made entirely of spinel, but are based on granular Al2O3 or granular MgO materials, with corresponding powdery or fine-grained spinel forming materials added to them to make them It is evenly distributed between the granular refractory materials. During the sintering process, a magnesia-aluminum spinel network is formed between the alumina particles, which plays a binding role. In addition, a small amount of boric acid or boric anhydride needs to be added to form a spinel network at a lower temperature (around 1300°C).
The best solution is for each steel casting enterprise to prepare its own furnace lining materials through experimental optimization and selection of the most appropriate ratio according to its own specific conditions. In this way, it can not only ensure long service life of the furnace lining and high metallurgical quality of the steel, but also significantly reduce production costs.
As for the composition ratio of the furnace lining materials, it should be selected based on the actual composition of the various raw materials used and determined through experiments. When determining the ratio of furnace lining materials, it can be calculated according to the following target components:
When using alumina as the basic particle material, keep the mass fraction of Al2O3 in the furnace lining material at about 85 to 88%, and the mass fraction of MgO at about 22%;
When using magnesium oxide as the basic particle material, keep the mass fraction of MgO in the furnace lining material at about 75 to 85%, and the mass fraction of Al2O3 at about 15 to 22%.