1.Refractory Classification
1, Refractory materials can be divided into 8 categories according to the chemical mineral composition: siliceous materials. Aluminum silicate material. Magnesium material. Dolomitic materials. Chromium material. Carbon materials. Zirconium Special refractories.
2, Refractory materials can be divided into 3 categories according to chemical properties: acid refractory materials. Neutral refractories Alkaline refractories.
3, Refractory materials can be divided into 3 categories according to the refractoriness: ordinary refractory materials, refractoriness of 1580-1770 degrees. Advanced refractory materials, refractoriness of 1770-2000 degrees. Special refractory materials, refractoriness higher than 2000 degrees.
4, Refractory materials according to the molding process can be divided into 7 categories: natural rock processing molding. Pressing molding refractories. Pouring molding refractories. Plastic molding refractories. Pounding molding refractories. Spray molding refractories. Extrusion molding refractories.
5, Refractories can be divided into four categories according to the heat treatment: fired brick. Unburned brick. Unshaped refractories. Molten (cast) products.
6, Refractories can be divided into 5 categories according to the shape and size: standard products. Universal products. Heterosexual products. Specialty products. Others, such as crucibles, dishes, tubes and so on.
7, Refractory materials can be divided into according to use: iron and steel industry with refractory materials. Refractories for non-ferrous metal industry. Refractories for petrochemical industry. Silicate industry (glass kiln, cement kiln, ceramic kiln, etc.) with refractories. Refractories for the power industry (power generation boilers). Refractories for waste incineration melting furnaces. Refractories for other industries.
2.Physical and chemical properties of refractory materials
1, Load softening point is characterized by the resistance of materials at high temperatures and under the joint action of the load, but also characterized by the softening temperature of the material showing significant plastic deformation; the point refers to the specimen in the continuous heating conditions to withstand a constant load and deformation of the temperature. Refractory bricks at room temperature compressive strength is very high, but at high temperatures and then pressurized will produce deformation, its compressive strength is significantly reduced. Refractory products per square centimeter of the area of 2 kg static load, and then heated, and gradually warmed up, when the refractory products undergo a certain deformation of the temperature becomes the load softening point. Therefore, the load softening point is also used to evaluate the high temperature structural strength of refractory products is an important indicator.
2, Thermal shock resistance, in the case of rapid changes in temperature refractory materials can not crack, do not flake performance is called thermal shock resistance, also known as cold and heat resistance, or resistance to rapid changes in temperature, or resistance to thermal disintegration, or thermal shock resistance, or thermal shock stability, and so on. The thermal shock resistance of various refractories can be measured according to standard YB376. Clay refractories have better thermal shock resistance, while magnesium bricks have slightly worse thermal shock resistance. Refractories as furnace lining and materials used at high temperatures, in addition to withstand high temperatures, in the process of use but also subject to periodic temperature changes, refractory resistance to rapid changes in temperature without damage to the ability of the refractory material is called refractory resistance to thermal shock or thermal shock stability, is the mechanical properties of refractory materials and thermal properties under the conditions of the temperature change of the integrated performance. Affected by the drastic changes in temperature will make the refractory products cracks, spalling or chipping damage caused by the poor thermal shock is the main reason for the catastrophic damage of the refractory lining under high temperature conditions. Therefore, the thermal shock stability of the material has an important impact on the service life.
3, Oxidation resistance, refers to the carbonaceous refractories in the high temperature oxidizing atmosphere to resist oxidation. Carbon-containing refractories have excellent slag resistance and thermal shock resistance, making them widely used in the metallurgical industry. However, carbon is easily oxidized, and once the carbon is oxidized, the performance of the product will no longer exist. Improving the oxidation resistance of carbon-containing products, especially at high temperatures, is an important part of the research on carbon-containing refractories.
3.Properties of commonly used refractory materials
Commonly used refractories: refractory bricks, high alumina bricks, castables, high alumina refractory bricks, heat preservation bricks, high alumina wear-resistant bricks, clay heat preservation bricks, lightweight high alumina bricks.
1, Acid refractories, with silicon oxide as the main component, commonly used silicon bricks and clay bricks. Silica brick is containing more than 93% of silicon oxide siliceous products, the use of raw materials such as silica, waste silica bricks, etc., its resistance to acidic slag erosion, high load softening temperature, repeated calcination volume does not shrink, and even a slight expansion, but it is susceptible to alkaline slag erosion, resistance to thermal vibration is poor. Silicon bricks are mainly used for coke ovens, glass kilns, acidic steel furnaces and other thermal equipment; clay bricks with refractory clay as the main raw material, containing 30% to 46% of the alumina, is a weakly acidic refractories, anti-heating vibration is good, acidic slag corrosion resistance, widely used.
2, Neutral refractories, with alumina, chromium oxide or carbon as the main ingredient. Containing more than 95% of alumina corundum products are a wide range of high-quality refractories. Chromium oxide as the main component of the chromium brick on the corrosion resistance of steel slag is good, but poor resistance to thermal vibration, high temperature load deflection temperature is low. Carbon refractories have carbon bricks, graphite products and silicon carbide products, its coefficient of thermal expansion is very low, high thermal conductivity, good resistance to heat vibration performance, high temperature strength, resistance to acid, alkali and salt erosion, not subject to metal and slag wetting, light weight. Widely used as high temperature furnace lining materials, also used as petroleum, chemical autoclave lining.
3, Alkaline refractories, magnesium oxide, calcium oxide as the main component, commonly used is magnesium brick. Containing magnesium oxide 80% to 85% or more magnesium bricks, alkaline slag and iron slag has good resistance, refractoriness than clay bricks and silica bricks high. It is mainly used in flat furnace, oxygen blowing converter, electric furnace, non-ferrous metal smelting equipment and some high temperature equipment.
4.commonly used refractory materials in the use of the process of combining (use) way
1, Hydration bonding – with the help of room temperature bonding agent and water hydration reaction to generate hydration products and produce bonding.
2, Chemical bonding – with the help of bonding agent and hardener, or bonding agent and refractory materials between the chemical reaction at room temperature, or when heated to generate a chemical reaction with the role of the bonding agent compounds and produce a combination.
3, Polymerization bonding – with the help of catalysts or crosslinking agents, so that the bonding agent condensation to form a network structure and produce bonding strength.
4, Ceramic bonding – refers to low-temperature sintering bonding, that is, in the bulk refractory materials can reduce the sintering temperature by adding additives or metal powders, in order to greatly reduce the temperature of the liquid phase, to promote the low-temperature solid-liquid reaction and produce low-temperature sintering bonding.
5, Adhesion bonding – is one of the following physical action with the help of several kinds of bonding. Physical adsorption: rely on the intermolecular interaction force – van der Waals force and produce the combination; diffusion: in the material molecules under the action of thermal movement, the binder and the molecules to be bonded to the molecular diffusion, the formation of the diffusion layer, thus forming a solid combination; electrostatic effect: the binder and the interface of the bonded material there is a Electrostatic effect: the interface between the binder and the bonded material has a double electric layer, and the bond is produced by the electrostatic gravitational force of the double electric layer. Cohesion bonding – rely on the addition of coagulant to make the microparticles (colloidal particles) cohesion and produce bonding.
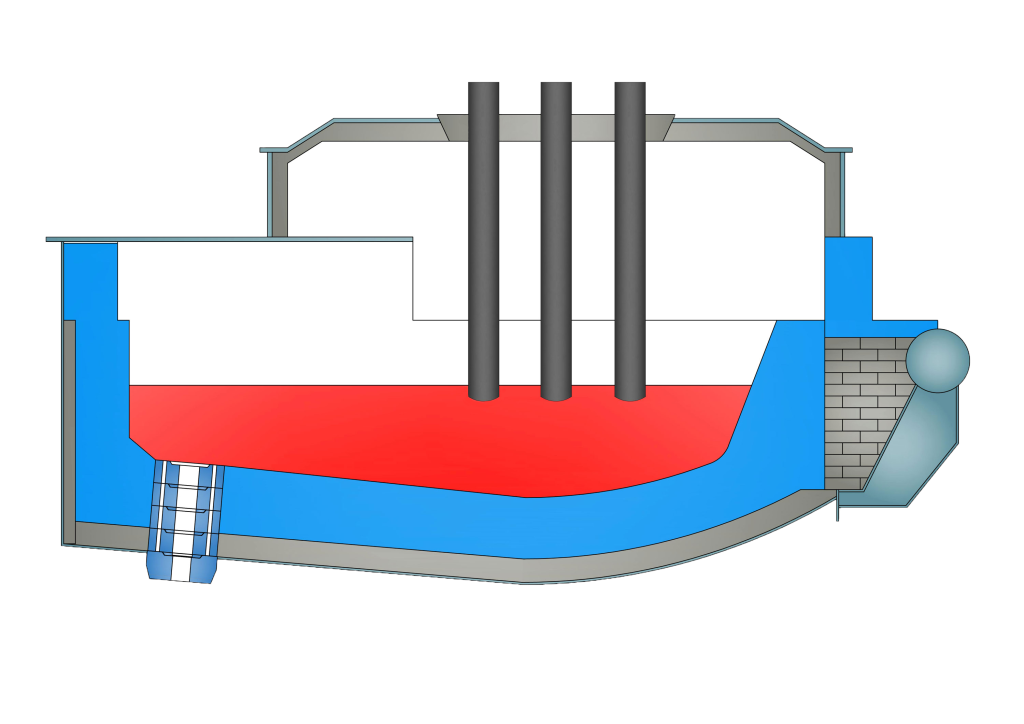