AOD converter smelting system basically consists of several parts such as furnace system, gas source device, dust removal system, material supply system and so on.
A complete furnace system is a complex linkage including furnace body, drag ring, tilting mechanism, suspension system. The following figure is a typical early AOD converter furnace.
Furnace body is divided into several parts, such as furnace cap, furnace shell, furnace lining working layer, furnace lining permanent layer, furnace bottom tamping material and so on. Furnace body working size requirements are: melt pool depth, slag surface or melt pool surface diameter, the ratio of the total height of the furnace chamber measured 1:2:3, the specific proportion of the size of the actual furnace capacity due to different furnace type and different.
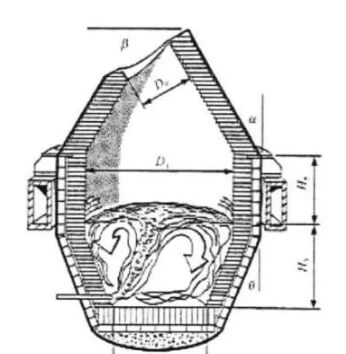
There are many factors affecting the life of the AOD converter, including the choice of furnace structure, masonry lining, smelting time, smelting temperature control, etc. According to a number of examples of analysis, the most important factors can be roughly divided into the refractory material impact and smelting process of the impact of these two major parts.
Due to the AOD converter stainless steel smelting production conditions are exceptionally harsh, resulting in its refractory consumption is much higher than ordinary steel. Generally speaking, the refractory material consumption of tons of ordinary steel is 9-12kg, while the consumption of stainless steel is 15-40kg.
Therefore, the selection of refractory material for the furnace lining must be strictly controlled, and the following standards and requirements must be met first:
(1) In terms of thermal stability, must be able to withstand sudden high-temperature thermal shock, with good thermal resistance, heat resistance, to ensure that in a wide range of temperature changes in the process, does not occur serious thermal spalling, thermal bursting.
(2) In terms of corrosion resistance, must withstand a variety of high-temperature chemical substances in the furnace thermal erosion, while ensuring that in a wide range of alkalinity changes can still maintain good thermochemical stability.
(3) In terms of mechanical properties, must have excellent mechanical shock resistance, abrasion resistance, in order to resist the violent turbulence of the molten steel, slag mixture eddy current of frequent impact wear.
Globally, the choice of refractories has gone through several iterations, from the early dolomite brick refractories, magnesium-chromium refractories to the current magnesium-calcium refractories.
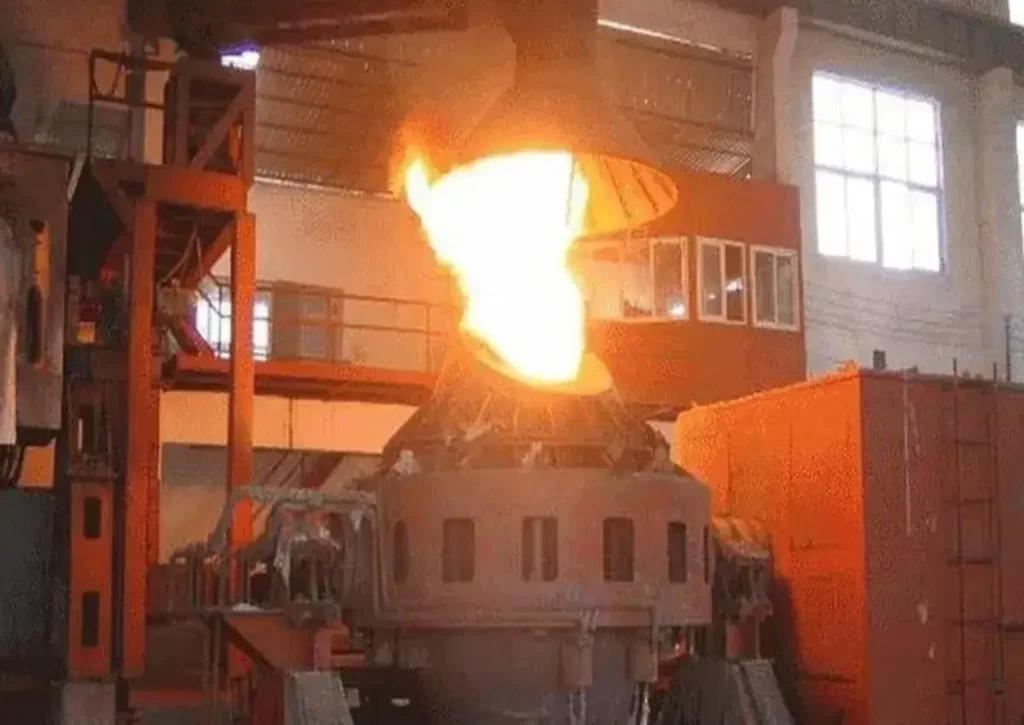
Magnesium-chromium refractories according to the processing materials and manufacturing process, can be divided into silicate bonded magnesium-chromium bricks, direct bonded magnesium-chromium bricks, fused magnesium-chromium bricks, magnesium-chromium bricks, not burned magnesium-chromium bricks, magnesium-chromium bricks again, pre-reaction magnesium-chromium turn, semi-reconjugated magnesium-chromium bricks, and so on.
Silicate bonded magnesium-chromium bricks with chromite and sintered magnesium sand as raw materials, sintered at high temperatures, due to good seismic properties, thermal stability, early was widely used in electric furnaces, cement kilns, flat furnaces and other equipment, but now has been basically for the direct bonded magnesium-chromium bricks to replace.
Directly bonded magnesium-chromium bricks are produced by firing chromite and sintered magnesia at a high temperature of 1700°C. The SiO2 content of chromite and sintered magnesia must be limited to a low range in order to allow direct bonding of the chromite and magnesite particles.
Re-bonded magnesium-chromium bricks with crushed fused magnesium-chromium sand as raw materials, through the second high-temperature sintering – re-bonded magnesium-chromium bricks with a uniform distribution of pores, a wide range of transient temperatures than the adaptability of fused bricks, heat-resistant than the direct bonded bricks stronger.
Pre-reaction magnesium-chromium bricks are made from magnesium-chromium sand, characterized by high strength at high temperatures, lower porosity than direct bonded bricks, and lower production costs than re-bonded bricks.
Semi-recombined magnesium-chromium brick is made of chromite, magnesium sand or pre-reacted magnesium-chromium sand and electrofused magnesium-chromium sand, and has the direct magnesium-chromium brick, magnesium-chromium brick or pre-reacted magnesium-chromium brick part of the properties of the overall performance to be superior to the direct magnesium-chromium brick, magnesium-chromium brick or re-reacted magnesium-chromium brick.
Fused magnesium-chromium bricks are made of chrome ore and magnesium sand, which have the characteristics of high strength, large pores, sensitive to temperature change and corrosion resistance.
Unburned magnesium-chromium bricks are made of chromite ore, sintered magnesium sand and a few chemical reagents, and are hardened by low-temperature heat treatment. Because it is often wrapped with iron in the process of molding, so it is also known as iron not burned bricks.
Magnesia-calcium series refractories based on different raw materials and processes, currently used in the AOD converter there are two main types, one is made of magnesia-calcium sand as the raw material of magnesia-calcium sand, and the other is made of magnesia sand, dolomite as the raw material of the dolomite brick. Although the two magnesium calcium refractory brick raw material composition is different, the production process also has differences, but in the use of performance, the two do not have a significant difference.
AOD converter early to magnesium-chromium refractory bricks, dolomite bricks as the main furnace lining masonry materials, but, with the magnesium-calcium refractory materials development technology development, magnesium-calcium refractory bricks performance is said to improve, the world’s current use of magnesium-calcium refractory materials in the A0D refining converter has become a trend – once magnesium-chromium refractory for the main masonry materials of the United States, in recent years, also The focus of attention gradually to the transition of magnesium-calcium refractory bricks, because compared with other refractories, magnesium-calcium refractory bricks have some of its unique advantages:
1) as its main chemical composition of MgO and CaO minerals have a high melting point, of which MgO melting point of 2800 ° C, CaO for 2570 ° C, in addition to the two lowest eutectic temperature of up to 2370 ° C, with good high temperature resistance, thermal stability.
2) The CaO component in the refractory material reacts with the slag to generate the intermediate product C2S and C3S will improve the slag viscosity, increase the wetting angle, which can greatly resist the slag on the refractory brick erosion and penetration, and appropriately increase the MgO purity and density, which can further improve the slag resistance of refractory material – at the same time, magnesium and calcium refractory material with good seismic, anti-flaking and other characteristics.
3) In the process of converter smelting, CaO in refractory bricks will adsorb sulfur, phosphorus, silicon dioxide, aluminum trioxide and other non-metallic impurities in the molten steel, enhance the purity of molten steel, and further purify the molten steel.
4) As the main raw material of magnesium-calcium refractory bricks, dolomite ore is abundant in our country, and the cost of mineral extraction is relatively low. At the same time, magnesium-calcium refractory bricks do not exist magnesium-chromium bricks similar to the chromium pollution problem.
More details about AOD Furnace
How does an AOD work?
The key feature in the AOD vessel is that oxygen for decarburization is mixed with argon or nitrogen inert gases and injected through submerged Tuyere air nozzles. This argon dilution minimizes unwanted oxidation of precious elements contained in specialty steels, such as chromium.
How does an AOD work?
Argon oxygen decarburization (AOD) is a process primarily used in steelmaking foundries and other high-grade alloys with oxidizable elements such as chrome and aluminum. In an AOD, metal is subjected to three steps of refining: decarburization, reduction, and desulfurization.
What is AOD in foundry?
Argon oxygen decarburization (AOD) is a process primarily used in steelmaking foundries and other high-grade alloys with oxidizable elements such as chrome and aluminum. In an AOD, metal is subjected to three steps of refining: decarburization, reduction, and desulfurization.
What is the full form of AOD furnace?
AOD stands for Argon Oxygen Decarburization, which is an advanced technology for the refinement of iron, nickel, and cobalt based alloys.