Reduce converter turnkey refractory consumption converter lining refractory use is directly related to the safety of the steel plant, operation and production, but also significantly affect the cost of steelmaking process, advanced steel mills and refractory suppliers will be the refractory consumption of the converter as one of the main indicators of its work. Converter refractory consumption level, the current more intuitive and scientific way of measurement for tons of steel consumption, that is, every production of 1t steel consumed by the number of converter lining and maintenance materials. Modern converter smelting process, the Japanese converter refractory consumption index can be controlled to 0.41~0.91kg/t steel (including masonry materials and maintenance materials). At present, WISCO refractory company contracted a steel plant in India 250t converter full service (8000 furnace) tons of steel consumption has reached 0.7kg/t steel. For the converter, the steelmaking concept, production rhythm, quality of converter lining, masonry construction, converter operation, optimization of magnesium-carbon bricks matching, daily maintenance and construction quality of converter, etc. are the keys to get lower refractory consumption.
Aiming at the high refractory consumption of 210t converter of a domestic steel plant contracted by WISCO, with the total refractory consumption of converter at 0.98kg/t steel, WISCO carries out a set of perfect optimization plan for converter contracting and formulates corresponding measures. Through the optimized design of converter type, matching of converter refractory materials and control of converter final slag, the total refractory consumption of converter was reduced to 0.87kg/t of steel.
Specific measures for converter optimization
1.Converter Furnace Optimization
The permanent layer of the 210t converter bottom of a steel plant is designed to be 195mm, the thickness of the magnesia carbon bricks of the bottom working layer is 800mm, the furnace volume ratio is 0.86m³/t, the working layer has a smooth arc transition from the center brick to the molten pool, and the center brick of the bottom is at the lowest position, as shown in Figure 1.
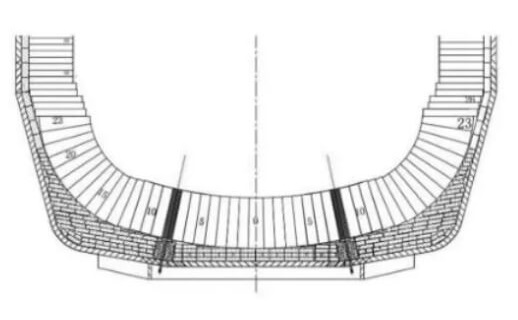
With the demand for steel purity of steel enterprises to improve, in recent years, the bottom of the converter blowing flow gradually increased, the converter furnace bottom running pressure, and from the center of the bottom of the furnace that is the beginning of the arc masonry, the periphery of the slope is larger, resulting in converter in the process of operation of the bottom of the converter from the center of the brick began to erode, and gradually diffuse to the bottom of the furnace 10 ring. The residual thickness of the converter is 600~700mm (including the permanent layer) at 3500 furnace, and the erosion rate is about 0.11mm/furnace, which leads to large maintenance consumption during the operation of the converter, and also affects the efficiency of the converter operation. The design of the working layer of the furnace bottom can not meet the smelting demand of the steel plant, so the furnace type is optimized and modified, and the design of the furnace bottom is shown in Fig. 2.
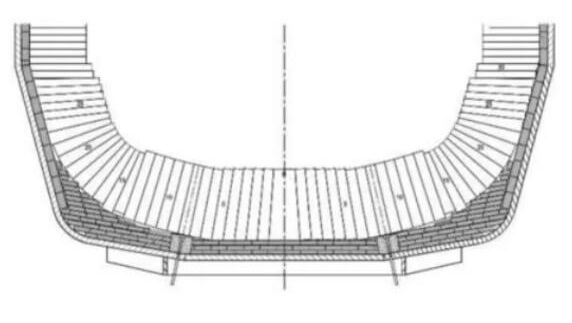
The furnace type was optimized and adjusted, and the working layer of the furnace bottom rings 1 to 13 was thickened to 1000mm. The shape of the furnace bottom rings 1 to 6 was designed as a “pan” type, and the working layer bricks were built closely to the permanent layer in a circular manner to the 6th ring of the furnace bottom, and the arc transition began slowly from the 7th ring. After the optimized design, the center brick is no longer the lowest point, and the entire bottom from the center brick of the furnace bottom to the 6th ring is flat, which jointly bears the stirring and static pressure of the molten steel.
2.Optimization of converter refractory matching
During the use of different converters, due to the influence of many factors such as different molten iron composition, smelting process, different steel grades and auxiliary equipment, some local areas of the converter erosion decreases too fast. In order to reduce the erosion rate during the operation of the converter and avoid the serious lack of residual thickness when the converter is offline as much as possible, the overall or local grades and materials are optimized during the design of the converter material.
Since its birth, magnesia carbon bricks have been widely used in various steelmaking kilns due to the non-wettability of graphite and slag and good thermal conductivity, making magnesia carbon bricks have excellent slag erosion resistance and thermal shock stability. The current national standard for magnesia carbon bricks (GB/T22589-2017) divides magnesia carbon bricks into 7 different carbon contents and 26 grades. At present, the main magnesia carbon bricks used in the general contractor converter of Wuhan Iron and Steel Refractory Company are: MT-10A, MT-12A, MT-14A, MT-16A, MT-18A. Since the smelting processes and steel types of different steel mills are different, it is particularly important to choose the magnesia carbon brick brand suitable for different steel mills. Domestic studies have shown that the decarburization layer thickness of ordinary magnesia carbon bricks is 2.4 times that of low-carbon magnesia carbon bricks. At the same time, compared with high-carbon materials, the distance between MgO particles in magnesia carbon bricks with low carbon content is small, and it is easy to form a MgO-rich reaction layer on the working surface of the material 4. After oxidation, magnesia carbon bricks are denser and have better oxidation resistance.
In view of this, the refractory company also carried out a series of verification tests on converter magnesia carbon bricks at carbon contents of 12%, 14% and 18%.
The steel smelted by a steel plant is mainly low-carbon steel (average steel C is 0.04%). The material matching scheme of the converter magnesia carbon bricks of a steel plant was determined through experiments, as shown in Table 2. The furnace bottom, front large surface and molten pool working layer need good anti-scouring performance due to the stirring of molten steel during operation, and the carbon content of magnesia carbon bricks is adjusted to MT-12A; the rear large surface magnesia carbon bricks need good oxidation resistance and corrosion resistance due to the long contact time with molten steel, and the material scheme is adjusted from MT-18A to MT-14A.
3.Converter final slag control
The use of high-quality converter refractory materials is the basis for the safe and smooth operation of the converter, and is also closely related to the appropriate converter operation and on-site maintenance. The Si, Mn, and P contents of hot metal with different compositions, the position of the converter smelting gun, etc., especially the slag splashing operation and proportion, the final composition and final slag control, will have a certain impact on the erosion of the converter lining.
The main substances that affect the melting point of converter slag are FeO, MgO and basicity. At present, the TFe of a certain steel plant is generally 15% to 20%. At a certain TFe ratio, the higher the basicity and Mg0% content of the converter final slag, the higher the melting point of the slag and the more viscous the slag. From the perspective of furnace protection, the more beneficial it is to the furnace lining. For cost considerations, the steel plant generally controls the converter basicity at 2.8~3.2. The basicity and MgO content of the 210t converter final slag of a steel plant before and after optimization are shown respectively. The basicity of the final slag before and after optimization increased from 2.9 to 3.3, and the MgO content of the final slag increased from 5.8% to 6.5%.
The slag splashing ratio and average slag splashing time of a 210t converter in a steel plant before and after optimization. After optimization, the converter started to splash slag to protect the furnace since the start of the new furnace, and the total slag splashing ratio in the whole furnace was 98.4%. The average slag splashing time was 2.68min, and the slag splashing ratio in the whole furnace increased by 14.8% compared with before optimization.
Application Effect
1.Decrease in erosion rate
A steel plant 210t converter before optimization of the whole furnace service furnace bottom thickness measurement data shown in Figure 6. The erosion rate of the furnace bottom is 0.046mm/furnace, and the thickness of the working layer of the furnace bottom is about 400mm at the time of the lower line. the converter erodes significantly faster within the range of 1.5m around the center brick at the pre-operation stage.
After taking a series of measures such as bottom furnace optimization, reasonable refractory matching and converter final slag control, 7525 furnace came off the line. The erosion rate is 0.037mm/furnace, erosion is significantly slower than before optimization, and there is no obvious decline in the center brick condition in the preoperating period of the converter, the bottom blowing element and the converter synchronous line.
2.Reduced maintenance consumption
After a series of measures were taken, such as furnace bottom type optimization, reasonable refractory matching and converter final slag control, the converter maintenance material consumption was reduced. The rear large surface maintenance material was reduced from 0.4kg/t steel to 0.35kg/t steel, a decrease of 0.05kg/t steel; the furnace bottom maintenance ton steel consumption was reduced from 0.25kg/t steel to 0.17kg/t steel, a decrease of 0.08kg/t steel. The total converter maintenance consumption was reduced by 0.13kg/t steel. The total maintenance consumption was reduced by 210t per furnace campaign.
3.Converter Utilization Efficiency Improvement
As the consumption of converter maintenance materials decreases, converter maintenance time decreases accordingly, and the proportion of converter maintenance time decreases. The maintenance time of the rear large surface is reduced by 41 hours, and the furnace bottom is reduced by 66 hours, saving a total of 107 hours of maintenance time. Due to the increase in the converter slag splashing ratio, an increase of 38 hours was caused, and the ratio of converter maintenance to total operating time decreased from 13.8% to 13.2%, and the converter utilization efficiency increased by 0.6%.
Effective measures
1、For a steel plant flat bottom type converter shell, the furnace bottom design for the flat bottom type furnace can slow down the erosion rate of the center of the bottom of the furnace, through the working layer of the bottom of the furnace bottom from 800mm thicker to 1000mm, and change the furnace type, the average erosion rate of the bottom of the whole furnace service from 0.11mm/furnace to 0.085mm/furnace, reducing the proportion of 22.7%.
2、For the converter of low carbon steel smelting, reduce the carbon content of magnesium carbon bricks in the bottom and rear face of the converter, can slow down the erosion of the bottom and rear face. For low carbon steel smelting converter, reduce the carbon content of magnesium-carbon bricks on the bottom and back face properly, which can slow down the erosion of bottom and back face.
3、 Adjust the alkalinity and MgO content of converter final slag appropriately, and increase the proportion of sputtering slag of the whole furnace to effectively reduce the maintenance of the converter.
4、 After adopting the optimization of the bottom type of the furnace, the reasonable refractory matching and a series of measures such as the control of the final slag of the converter, the total consumption of maintenance of 210t converter of a certain steel plant decreased by 0.13kg/t of steel in total.
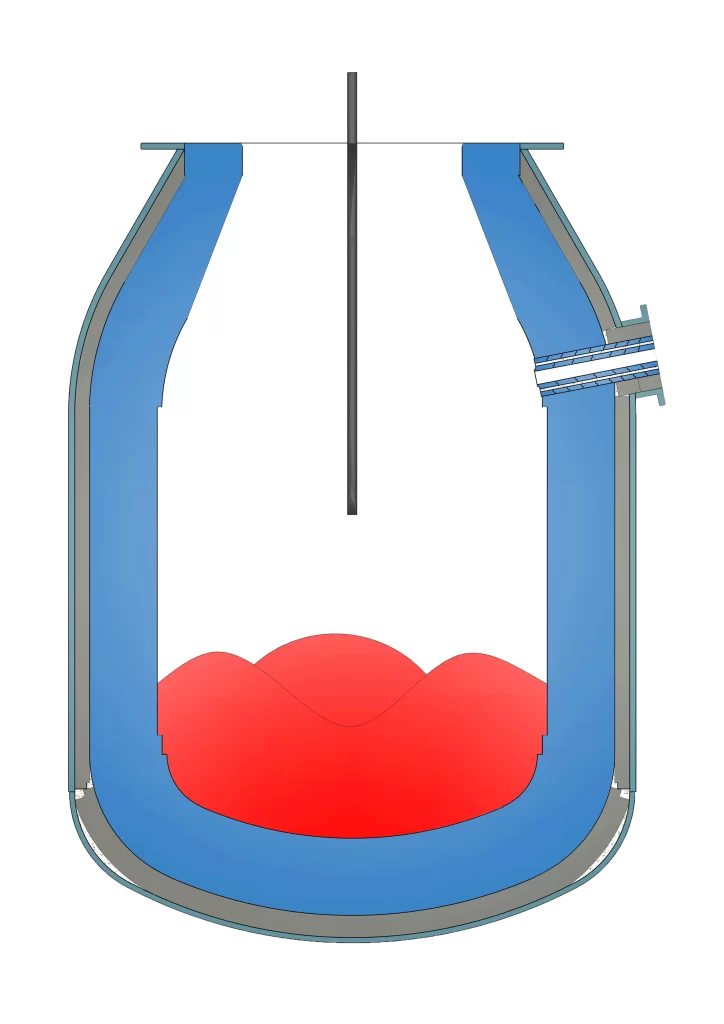