It can be seen from the process flow chart that the production process of magnesium carbon bricks is not complicated, but to produce high-quality products, each process must be strictly monitored, including mixing, moulding, heat treatment (drying) of these links is particularly important in the production of the place.
1.Breaking and crushing
Broken crushing is the process of processing large materials into ideal particle size material. Is an essential process in the production of refractory materials, although simple, but very important, it has an important impact on the stability of product quality. At the same time crushing equipment power consumption, wear and tear, high maintenance rate, so high maintenance costs. Emphasis on broken crushing, stable product quality, energy saving and consumption reduction.
The process of producing magnesium carbon bricks broken crushing purpose is mainly to prepare a variety of different particle size of raw materials. Increase the specific surface area of the material and destroy the material lattice, so that it produces defects, thereby accelerating the physical and chemical reaction speed of the material.
2.Batching(Weighing)
Batching is the process of combining different raw materials and different particle compositions according to the product formula design. The method of dosing varies according to the type and state of the raw material.
The process of producing magnesium-carbon bricks usually adopts the weight batching method, because the accuracy of the weight batching method is high, usually not more than 2 per cent. Commonly used weight batching equipment includes manual weighing scales, automatic weighing scales, weighing trolleys, etc. The appropriate equipment is selected according to the requirements and the level of automatic control.
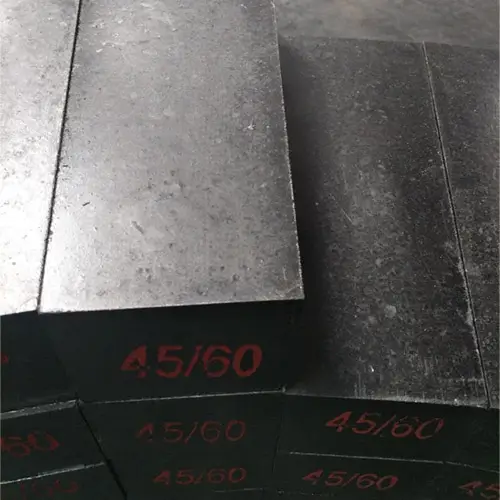
3.Preparation of clay (mixing and training)
The purpose of mixing is to make the material composition uniform, and the contact surface between different materials is expanded as much as possible. The mixing of refractory materials is a method of homogenising the material along with squeezing, kneading and venting processes. With any powder mixing, refractory material mixing is also a step-by-step process, and because of the material components, particle size, combining agent and additives of different, so that the mixing process is more complex.
There are many general categories of magnesium-carbon bricks, and the formulas are different according to the parts where they are used, mainly the taste of magnesium sand, the amount of graphite added, and the types and quantities of additives will be changed. For example, in the slag line part of the ladle, in order to improve the slag resistance and thermal shock stability of magnesium carbon bricks, the taste and addition of graphite will have to be increased. If the carbon content is small 10%, the internal magnesium carbon bricks can not form a continuous carbon network, the characteristics of carbon can not be fully played, affecting the magnesium carbon bricks slag resistance and thermal shock resistance stability. And if the carbon content is too high, not only will bring difficulties to the production of magnesium carbon bricks, but also make magnesium carbon bricks easy to oxidise. Therefore, the carbon content in magnesium carbon bricks is generally controlled between 10% and 20%.
In order to make the magnesium sand particles can be evenly wrapped by graphite, the mixing is generally carried out according to the following steps, first of all, granular material, then add resin, then add graphite, and finally fine powder and various additives. Graphite density is small, easy to float, and add a large amount, so it is not suitable for mixing, and additives to add a very small amount, so you want to mix the whole material evenly, must be a long time high intensity mixing. However, the binding agent will volatilise and become dry during the mixing process, and too long a time will cause the graphite and fine powder wrapped around the particles to fall off, so the mixing time must be controlled.
4.Moulding
Forming is an indispensable process for the production of shaped refractory products, which is the process of refractory clay becoming a billet with a certain shape and strength under the joint action of pressurised equipment and moulds.
Refractory materials have a variety of moulding methods, magnesium carbon bricks are used in semi-dry pressing and moulding. Semi-dry moulding is not too strict on the requirements of the mud, the process is simple, the pressurisation process, due to the low moisture content of the mud, it must be used to force a large pressure to force its particles to close the combination between the particles. Under the action of external force, the particles are rearranged, the gas is discharged, the particles are combined and then produce strength to form a blank with a certain shape. Semi-dry moulding is the most important factor is the applied pressure, within a certain pressure range, the size of the applied pressure directly determines the performance of magnesium carbon bricks. With the increase of pressure, the density of billet increases, porosity decreases and strength increases.
Magnesium carbon bricks with excellent performance have a commonality, that is, magnesium carbon bricks with high bulk density and low porosity. The magnesium-carbon bricks with an opening porosity of less than 4% have a very low erosion rate.
The purpose of forming is to make the magnesium carbon brick organisational structure densification, due to the magnesium carbon brick forming is used semi-dry method, so it must be large pressure forming. Due to the small particle size of the clay used for moulding and the high graphite content, the moulding should be operated in strict accordance with the protocol, otherwise it is easy to produce cracks or layer cracks. Should be first light and then heavy, many times pressure, light hammer exhaust slow down, heavy hammer pressure slow lift.
If there are conditions can be used vacuum pumping brick press, pressurised before the mud in the mould cavity to vacuum, pressurised without the need to exhaust, so that even if the speed of light hammer pressurisation is accelerated, it is almost impossible to make the magnesium-carbon bricks produce cracks or layer cracks. It is especially useful for high-carbon magnesium-carbon bricks, which are prone to layer cracking.
5.Heat treatment (drying)
Magnesium carbon brick heat treatment, usually the factory called this process drying, in essence, drying used here is not accurate enough, because drying is generally mainly refers to the product contained in the moisture discharge process. And magnesium carbon brick heat treatment process in addition to contain the discharge of water, but also accompanied by a series of physical and chemical changes, so we call this process called heat treatment.
The heat treatment temperature of magnesium carbon bricks has a direct impact on the performance of magnesium carbon bricks. The heat treatment process of magnesium carbon brick is actually the process of curing phenolic resin, heat treatment temperature and heat treatment time directly determines whether the phenolic resin is completely cured, within a certain range, the resin completely cured time and curing temperature is inversely proportional to the curing temperature, but not a straight line relationship.
Through experimental research shows that magnesium carbon bricks only in a certain temperature range for heat treatment, the density can reach the best, if the heat treatment temperature is lower than this temperature range, the density of magnesium carbon bricks will be reduced, but if higher than this range, the density of magnesium carbon bricks will fall very quickly. After repeated research shows that the more reasonable temperature range is 200 ℃ ~ 250 ℃.
From the flow chart to see the impact of magnesium carbon brick performance process factors are many, there are raw materials selection, particle size ratio, mixing the quality of the material, the size of the pressure, etc., the following we analyse these factors one by one, to see how to both economic quality and stability of the product.
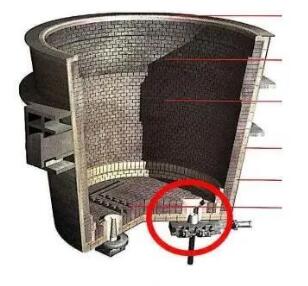