Ladle purging plug play an important role in the process of molten steel refining. As a refractory product, there will be consumption and damage during use. If the use method is not properly grasped, it will affect normal production and even cause serious production accidents such as steel breakout.
The purging plug is located at the bottom of the ladle, and must withstand the static pressure of the molten steel during use. When the residual length of the brick core is too short, the direct connection area between the brick core and the seat brick will decrease, and the strength of the brick core will also decrease. Cracks are prone to appear under the influence of rapid cold and rapid heat. If the pressure that the brick core can withstand is less than the static pressure of the molten steel, the brick core will be pressed to fall off, or the molten steel will penetrate through the cracks in the brick body, resulting in a leakage accident.
Cause Analysis
The purging plug is gradually consumed during use, and the length becomes shorter and shorter. If the safety limit is exceeded, the purging plug will leak. The erosion rate of ladle permeable bricks is within the range of 5-10mm, which is mainly affected by the production process, steel type and the oxygen burning habits of workers.
Another way to express the life of purging plug is the blowing time. The extended single use time of the same ventilating brick will also reduce the number of times the ventilating brick is used.
In specific use, most customers only care about the service life of the ladle, and ignore the total argon blowing time of the ventilating brick. In addition, the methods for judging the residual length of ventilated bricks are not the same, and many methods are not sweet and accurate, which leads to excessive use of ventilated brick cores, resulting in excessively short residual lengths.
Solution: Design a safety display device. Generally, safety display signs are installed at the lower part of the ventilating fire brick about 150mm. The appearance and brightness of the material in the hot state and the ventilating brick are obviously different, which is easy to judge. When you see the safety display during use, immediately take it off the assembly line, which can effectively avoid the leakage accident caused by the short ventilating brick.
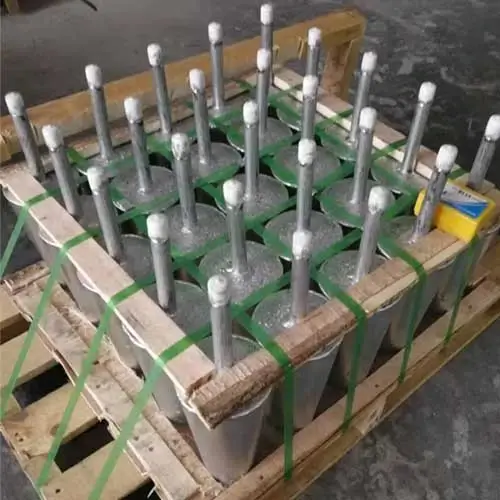
More details about Ladle purging plug
What is purging in ladle?
Dual gas purging is often done in a ladle to accelerate the refining operations in steel industries. The purged gas, mainly argon imparts momentum to the molten metal and establishes a turbulent recirculating flow in the melt, which generates shear stresses on the ladle walls.
What are the different types of purging plugs?
There are two types of purging plugs, porous plug which is focused more on a reliable bubbling, and slit plug (through-bore type) which is more focused on service life. However it is essential to develop the good characteristic of it, and reduce the week point of both types.
Why argon is purged at the bottom of the ladle?
During ladle refining process, argon gas is purged into the ladle for stirring the molten steel bath to eliminate thermal and composition gradients and to achieve inclusion flotation. Operating parameters like purging location, porous plug configuration and argon flow rate primarily affect liquid steel refining.
What is argon purging in steel making?
Steel ladle during the argon purging process. The production of high-quality steel requires purging with argon to remove impurities, degas the molten metal, and optimize the alloying process. However, sealing challenges in steelworks result in variable argon losses. But accurate mass flow measurements are crucial for process optimization.