By analyzing the composition of refractory materials in the tundish and the refractory damage problems that occur in daily work, we have identified the causes and proposed solutions to ensure the safe use of refractory materials. In continuous casting, a tundish is used to hold and transfer molten steel. The molten steel from the ladle stays, calms, and is kept warm. Finally, it is distributed to the crystallizer through the water inlet in the tundish one by one, completing the conversion of molten steel into steel billets. The part of the tundish that contacts the high-temperature molten steel is mainly refractory materials, and the quality of the refractory materials directly determines the life of the tundish and the quality of the molten steel. For different smelting processes, the configuration and requirements of the refractory materials in the tundish are also different.
The interior of the tundish is composed of high temperature resistant materials. Different smelting processes require different tundish shapes and different refractory configurations. The commonly used tundish shapes are “T”-shaped single tundish and knife-handle-shaped double tundish. The internal refractory configuration is designed with different materials according to the use requirements of the tundish and the particularity of the smelting steel. Generally, the permanent layer is casted with castables, and the working layer is formed by vibrating and ramming magnesium dry materials.
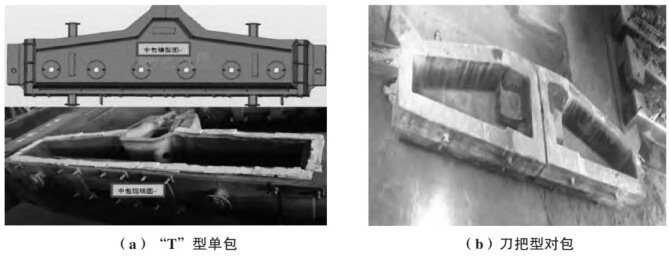
The capacity of the molten steel in a conventional tundish is generally 20% to 40% of the ladle. The outer shell of the main body is welded and assembled by steel plates, and the lining of the ladle is composed of refractory materials.
The refractory materials in the tundish mainly include the tundish body, the tundish cover, the stopper rod for controlling the flow rate of the molten steel [some use sliders (also known as down-flow nozzles) to control the flow], and the water inlets through which the molten steel flows [upper water inlet seat bricks, upper water inlet, lower water inlet (also known as sliders), immersed water inlet]. The connection between the ladle and the tundish is connected by a large ladle protection sleeve. The molten steel flows out from the bottom of the ladle and flows into the tundish through the large ladle protection sleeve, which is also called protective pouring. Some companies do not use large ladle protection sleeves, commonly known as naked pouring. In order to deal with the damage to the refractory materials at the bottom of the ladle caused by the molten steel flowing down from a certain height, an impact zone is set directly below the molten steel, and an impact plate or a flow stabilizer refractory is used to withstand the strong impact force of the molten steel at the beginning.
During the use of the bag-type tundish, areas where accidents are prone to occur include: the slag line of the tundish, around the impact zone, and the water inlet.
1.Tundish slag line
The dry material at the slag line of the tundish is not resistant to erosion and scouring by molten steel, especially when production is unstable, there is a low liquid level pouring phenomenon on site, and the slag line position changes, resulting in leakage accidents.
The main reason is that the refractory materials in the tundish are not baked properly, especially in winter, the moisture in the gas is not completely removed, the baking time is short, and the strength of the dry material in the working layer of the tundish does not reach the required strength.
2.Around the impact zone of the tundish
The protective plates around the impact zone of the ladle-type tundish are prone to fall off and collapse, which causes the molten steel to erode the permanent layer and cause the ladle to leak steel.
The main reason is that when the molten steel in the ladle is initially poured, the position of the ladle and the tundish is not centered, causing the two water inlet steel flows of the ladle and the impact zone of the tundish to be not centered, causing the molten steel to deviate to the position of the protective plate of one of the tundishes, causing the protective plate to be damaged, collapsed, and peeled off. Figure 4 shows the situation where the steel flow is not centered when the large ladle protection sleeve is not used at the beginning of pouring.
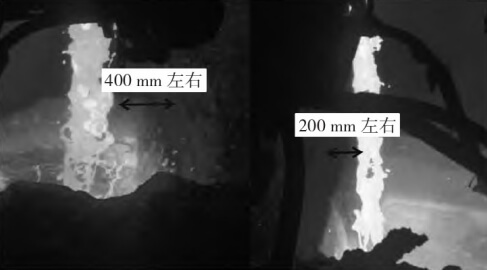
3.Tundish water inlet
The service life of the tundish upper nozzle is short. The main reason is that during the process of gradually increasing production on site, the zirconium core inside the nozzle is not resistant to erosion by molten steel, and the diameter is severely expanded, causing the lower nozzle to turn red and leak, resulting in a tundish penetration accident.
4.Tundish baking
The baking of the tundish is divided into offline baking and online baking, all of which use conventional blast furnace gas burners. On-site offline baking (with mold) is shown in Figure 6: There is a baker on the tundish. During normal combustion, the gas enters from the middle nozzle on the upper part of the burner, and the air (oxygen) enters from the side nozzle to ensure complete combustion of the gas. According to the flame combustion situation, adjust the ratio of gas and air (oxygen) at any time, lengthen the burning flame, and descend to the bottom of the tundish to bake the bottom of the tundish. The normal baking time is about 2 hours. In winter, according to the hardening degree of the dry material and the size of the flame, the baking time can be appropriately extended to 3 to 4 hours.
Baking on the tundish continuous casting platform (online baking) is carried out according to a certain baking system. Different baking systems are adopted according to different tundish shapes and material configurations. First, clean up the debris in the tundish and the debris in the nozzle. Observe from the on-site nozzle. The best time is when the flame in the tundish descends to the nozzle.
Some enterprises, according to the on-site conditions, set up a reverse suction device from the lower water outlet to suck the flame in the tundish downwards, so that the flame and heat in the tundish can fully reach the lower water outlet; some enterprises directly install the submerged water outlet, and use the reverse suction device to suck the flame in the tundish downwards, and reach the submerged water outlet through the upper water outlet and the lower water outlet.
For the baking of the tundish (using blast furnace gas), the key management points are as follows:
(1) Before baking, clean the residue in the tundish and nozzle to ensure that the nozzle can be effectively baked.
(2) Check whether the pressure of various gas sources (gas, compressed air) of the baking machine has reached the specified pressure and whether various instruments are intact.
(3) Use an open flame to aim at the nozzle of the baking machine, or place firewood in the tundish to burn, open the main gas valve, air valve, and gas valve in sequence, ignite each gas burner in sequence, and adjust the air-gas ratio to ensure that the gas is fully burned.
(4) During the baking process, workers should always stand at the upwind position to monitor and observe the burning of the burner at any time. If the flame is out, turn off the gas in sequence, then close the valves, find out the cause, and start from the above steps to re-ignite.
Blast furnace gas baking can be carried out in three stages, and the baking time is controlled to be more than 5 hours. The specific baking standards are as follows:
The first stage: low-fire baking (<800℃) for more than 120 minutes (the time can be extended as needed).
The second stage: low-fire heating to medium-fire (800-1000℃) for more than 60 minutes.
The third stage: high-fire baking (1000-1050℃) for more than 90 minutes before pouring steel.
The precautions during the baking process are as follows:
(1) In principle, the high-fire baking time should not exceed 6 hours, because at this time the dry material has a low strength and a large thermal expansion, which may cause the package to collapse. According to the actual situation on site, after baking with a high fire, it is not allowed to switch to a low fire for repeated baking, otherwise it is easy to cause cracks and embrittlement of the dry material.
(2) When the temperature rises too quickly from a low fire to a medium fire, the gas in the package wall cannot be effectively removed, which will cause large-area cracks in the package wall and severe separation. The severe separation of the intermediate package may cause the package to collapse and reduce the overall quality and strength of the refractory material during use.
(3) When baking with a high fire, a slight separation of the package wall (less than 20 mm) does not affect normal use. At the same time, the ratio of air to gas should be strictly controlled during the baking of the package.
5. Improvement of the tundish nozzle
The service life of the tundish nozzle is short, mainly because the aluminum-carbon material on the outside of the zirconium core of the tundish nozzle has poor resistance to the impact of molten steel. After the casting speed is increased during continuous casting (the diameters of the upper and lower nozzles are expanded at the same time), the aluminum-carbon refractory material on the zirconium core of the upper nozzle and the outside of the zirconium core decreases as the flow rate of molten steel increases. According to the on-site conditions, the aluminum-carbon material on the outside of the zirconium core of the tundish nozzle is improved, mainly by improving the material, increasing the compressive strength, and improving the impact resistance of the aluminum-carbon material on the outside of the zirconium core nozzle; at the same time, the zirconium core inside the nozzle is improved, and the outer diameter of the zirconium core inside the upper and lower nozzles is expanded by 10 to 20 mm [1].
After the improvement, the service life of the tundish nozzle is improved, and the redness of the lower nozzle is no longer observed.
6.Strengthening the daily management of intermediate packages
(1) Select appropriate tundish refractory materials according to the working conditions of the tundish. For smelting ordinary steel grades, choose long-life refractory materials to increase the service life of the tundish and reduce process costs; for smelting special steel grades, use special refractory materials, you can choose economical tundish age, improve the cleanliness of molten steel, and improve the quality of molten steel.
(2) The tundish should be clean and tidy without debris. For cold shrinkage cracks generated during offline baking, you can use the coating construction method to rectify.
(3) For the tundish with a knife-handle type, the bottom of the ladle is generally used with an impact plate and the side is used with a guard plate to form a pouring area. This area is subject to the greatest impact force of the molten steel when the tundish is poured. Corundum mullite or silicon carbide refractory materials are usually selected; for the “T” type single ladle, a flow stabilizer is generally used, and high-aluminum mullite refractory materials are usually selected.
(4) The tundish needs to be monitored and managed throughout the process. The ladle turntable must be adjusted at any time when the ladle is being poured to ensure that the steel flow is centered and to prevent the molten steel from washing the refractory in the impact zone, causing the guard plate to erode too quickly and reduce its life. Any abnormal conditions that occur during the use of the tundish should be analyzed and adjusted in a timely manner.
(5) Make good use cards and records for the tundish to facilitate analysis and summary after the tundish is offline.
For the steelmaking process in steel enterprises, the tundish pouring steel process in the continuous casting system has a high consumption of refractory materials, and it is necessary to consider increasing the number of multi-furnace continuous casting times, while adopting new technologies and selecting cost-effective refractory manufacturers; further study the erosion mechanism of refractory materials in the tundish pouring steel system, explore the erosion laws of its various parts, improve the use conditions of continuous casting refractory materials, increase their service life to reduce costs, and ultimately improve the safety production coefficient and steel product quality.