Refractory castable is a new type of refractory material that has good fluidity after adding water and stirring without calcination. It is an important variety of amorphous refractory materials. It is a mixture composed of refractory aggregate, refractory powder and binder (or other additives) in a certain proportion. It can be shipped in bulk form or made into prefabricated parts.
Refractory castables can usually be classified according to the type of binder, type of refractory aggregate and porosity. According to the type of binder and the bonding method, it can be divided into:
① Hydration bonded castables, such as silicate cement bonded refractory castables; aluminate cement bonded refractory castables; ρ-Al2O3 bonded refractory castables.
② Hydration bonded and coagulation bonded castables, such as low cement bonded refractory castables and ultra-low cement bonded refractory castables.
③ Coagulation bonded castables, such as clay bonded refractory castables, ultrafine powder bonded refractory castables, silica sol or alumina sol bonded refractory castables.
④ Chemical bonded castables, such as water glass bonded refractory castables, phosphoric acid and phosphate bonded refractory castables, polyphosphate bonded refractory castables, sulfate bonded refractory castables and phenolic resin bonded castables.
According to the refractory raw material varieties are divided into siliceous, semi-siliceous, clay, high aluminum, corundum, magnesium, spinel, and special aggregate refractory castable base (special aggregate includes silicon carbide, chromium slag and zircon, etc.), and according to the porosity of the dense castables and lightweight castables.
Portland cement bonded refractory concrete
Silicate bonded refractory castables are made of ordinary silicate cement, slag silicate cement and silicate heat-resistant cement as binder, and formulated with refractory aggregate and powder. Its use temperature is 700-1200 ℃, can be used for the whole load-bearing heat-resistant structure and kiln lining, especially in the thermal equipment foundation and base plate flue, chimney lining, and hot storage tanks and other engineering applications.
Aluminate cement bonded refractory castable
According to the type of binder, it can be divided into alumina cement refractory castables, aluminum-60 cement refractory castables, low calcium aluminate cement castables and pure calcium aluminate cement refractory castables. Alumina cement refractory castables have the characteristics of fast hardening, high strength, good thermal shock stability and high refractoriness. Therefore, they are widely used in general industrial kilns and thermal equipment in industrial sectors such as metallurgy, petrochemicals, hydropower, building materials and machinery. Its maximum operating temperature is 1400-100℃, and some can reach about 1800℃. A. Ordinary aluminate cement bonded refractory castables. The commonly used binders for ordinary calcium aluminate cement bonded refractory castables are alumina cement, aluminum-60 cement and low calcium aluminate cement.
The main mineral of alumina cement is calcium aluminate, which has a fast hydration speed and does not precipitate calcium hydroxide. Therefore, the refractory castable prepared by alumina cement has the characteristics of fast hardening and high strength. In order to improve its performance, high-quality refractory aggregates and powders can be selected, and measures such as adding micropowder to reduce cement dosage and adjusting particle grading can also be adopted.
Compared with alumina refractory castables, aluminum-60 cement and low calcium aluminate combined refractory castables have the characteristics of high refractoriness, good thermal shock resistance, and strong slag resistance. They are widely used in the high temperature section of the heating furnace system, as well as the furnace cover of the electric furnace, vacuum nozzles and rotary kiln linings. The main mineral composition of aluminum-60 cement and low calcium aluminate refractory cement is monocalcium dialuminate, which has a slow hydration rate. This type of refractory castable is cured at room temperature, with low early strength and high later strength. If steam curing can be used at a higher temperature, the purpose of rapid hardening and high strength can be achieved.
B low cement series refractory castable
Low cement series refractory castables refer to castable refractory materials with calcium aluminate cement added in an amount less than 8%. The CaO content in the castable is required to be less than 2.5%. Its main varieties include low cement (CaO content 1%~2.5%), ultra-low cement (CaO content less than 1%) and cement-free (CaO content less than or equal to 0.2%) refractory castables, which have the characteristics of high density, low porosity, high strength, low wear, thermal shock resistance and erosion resistance, as well as strong volume stability and low construction water consumption. According to its material variety, it can be divided into low cement series refractory castables such as aluminum silicate, mullite, corundum, magnesia aluminum, shale, carbon and silicon carbide. According to its use, it can be divided into blast furnace tapping ditch refractory castables and steelmaking ladle refractory castables.
The application of micropowder and ultrafine powder and admixtures is one of the key technologies of low cement series refractory castables. The mechanism of coagulation and hardening is the result of the combined action of cement hydration and powder coagulation. It is characterized by high strength, and the strength increases significantly with the increase of heating temperature. The air permeability of the castable is poor, and it is easy to cause peeling or cracking during baking. The baking system should be reasonably formulated according to its variety, construction thickness and location. At the same time, explosion-proof agents such as metal aluminum powder, aluminum lactate and organic fiber can also be added to the refractory castable.
Ultra-low cement refractory castables are developed on the basis of low cement refractory castables. The amount of aluminate cement is generally 2.5%~5%, and the CaO content in the castable should be between 0.2% and 1%. The preparation principle and strength change characteristics are basically the same as those of low cement refractory castables, but its performance is better than that of low cement refractory castables. There are many varieties of ultra-low cement refractory castables and they are widely used. Ultra-low cement combined with Al2O3-SiC-C castables are commonly used in blast furnace tapping channels at home and abroad. This type of castable is generally made of dense white corundum, sub-white corundum, brown corundum, high-quality high-aluminum clinker, silicon carbide, asphalt, flake graphite and other materials, and then mixed with ultra-fine powder, binder and admixture. High- and medium-range products are suitable for tapping channels of large and medium-sized blast furnaces, while medium- and low-end products are suitable for tapping channels or slag channels of medium and small blast furnaces.
C cement-free refractory castable
Ultrafine powder bonded refractory castable is a cement-free refractory castable developed on the basis of ultra-low cement refractory castable. Due to the low CaO content in this castable, it has excellent high temperature performance. Its varieties include aluminum silicate, corundum, mullite, magnesia, aluminum magnesium, aluminum magnesium spinel, etc. n Coagulation and hardening is achieved by the coagulation and bonding of ultrafine powder to obtain strength. Its preparation principle and strength change characteristics are basically the same as those of low cement refractory castable.
ρ-Al2O3 bonded refractory castable is a cement-free refractory castable with ρ-Al2O3 as a castable binder. The biggest feature of ρ-Al2O3 as a castable binder is that it does not contain CaO. Therefore, this castable has superior high temperature performance than pure calcium aluminate cement bonded castable. ρ-Al2O3 forms Al(OH) after hydration, and Al00H can play a role in cementation and hardening.
Water glass combined refractory castable
Waterglass combined refractory castable is an air-hardening refractory material that uses waterglass as a binder and is mixed with various refractory aggregates in a certain proportion. It has the characteristics of less strength loss under high temperature, better thermal shock resistance, better high-temperature wear resistance and better high-temperature corrosion resistance. Therefore, it is often used in some parts with special requirements. Its maximum use temperature varies with the type of refractory aggregate and powder used, the type of coagulant and the molding method. Waterglass combined castables are divided into aluminous, clay, semi-silica, siliceous, magnesia, magnesium-alumina, etc. according to the type of aggregate. In the thermal equipment of metallurgy, petrochemical and other departments, clay, high-alumina, semi-silica and magnesia waterglass combined castables are widely used. The waterglass modulus used in ordinary waterglass refractory castables is 2.3-3.0, the density is 1.30-1.40/cm3, and the coagulant is usually sodium fluorosilicate, and silicate cement is also used. The amount of waterglass is 12%-17%. Sodium fluorosilicate accounts for 10% to 15% of the mass of water glass. The general properties of water glass bonded castables are shown in the table below. The refractoriness and load softening temperature of this castable are low, so the long-term use temperature is generally 1000℃, and the maximum use temperature is not more than 1400℃. To increase the use temperature of water glass bonded refractory castables, comprehensive technical measures need to be adopted: using modified water glass as a binder, controlling the modulus, density and dosage of water glass binder, and improving the grade and fineness of the matrix material.
Water glass bonded aluminum-magnesium refractory castables are made of high-alumina bauxite clinker as aggregate, high-alumina bauxite clinker and magnesia sand as powder or adding part of synthetic spinel, and water glass as a binder. It is used as the integral lining of steel ladle, iron ladle and steel spout. Aluminum-magnesium refractory castables are divided into three grades according to physical and chemical indicators: LMJ10, LMJ45 and LMJ-65. Its physical and chemical performance requirements are shown in the table.
Phosphoric acid and phosphate bonded refractory castables
Phosphoric acid and phosphate refractory castables are new refractory materials with good performance, which are prepared by phosphoric acid or phosphate solution with refractory aggregate and powder in a certain proportion. Commonly used binders include phosphoric acid, aluminum dihydrogen phosphate, polyphosphates, etc.
Phosphoric acid and aluminum phosphate combined refractory castable
According to the type of binder, it is divided into phosphoric acid combined refractory castables and aluminum phosphate combined refractory castables. The refractory aggregates and powders used are usually alumina clinker, clay clinker, magnesia, waste silica bricks or silica, corundum, mullite, silicon carbide, etc. Light aggregates include expanded perlite, hollow alumina balls, etc. According to the type of aggregate, it can be divided into high alumina, clay, siliceous and magnesian.
Phosphoric acid or aluminum phosphate reacts only slowly with neutral and acidic aggregates (such as waste silica bricks or silica) at room temperature. In order to promote the hardening of castables at room temperature, hardeners such as alumina cement, calcium aluminate cement, magnesium oxide, etc. are often used. Phosphoric acid or aluminum phosphate reacts with the iron contained in the raw materials used to affect the aging change, and it also corrodes the mixer when mixing the mud. Therefore, aging inhibitors are often added during batching, such as adding 0.15% NH-66 inhibitors. If no inhibitor is added, the material should be trapped after stirring. In addition, phosphoric acid and phosphate combined refractory castables should not be cured with water or steam.
Phosphoric acid and phosphate combined refractory castables are characterized by good thermal shock stability, high compressive strength, strong resistance to slag corrosion and impact, high load softening temperature and chemical stability. Its use temperature varies depending on the type and grade of the raw materials, ranging from 1000 to 1800°C.
Sodium polyphosphate combined refractory castable
When magnesium materials are used as refractory aggregates and powders, because the reaction between phosphoric acid and aluminum phosphate solutions and magnesium materials is intense, the mixture sets quickly and there is no construction time, so sodium polyphosphate is used as a binder. Commonly used ones are sodium tripolyphosphate and sodium hexametaphosphate. Magnesium refractory castables are easy to hydrate. Cracks are easy to form during the drying process. Adding an appropriate amount of silicon oxide powder can overcome the hydration problem, but the amount of silicon oxide added should be controlled as it affects the high temperature performance of the material. Aluminum-magnesium or alumina-spinel refractory castables are castables developed for ladles. The refractory aggregates are corundum and special alumina clinker, the powders are magnesium-aluminum spinel powder, alumina clinker powder, corundum powder and magnesia powder, etc. The binders are silicon oxide powder and sodium polyphosphate.
Clay bonded refractory castables
Clay-bonded refractory castables are castable refractory materials made of soft clay as a binder, bauxite clinker, clay clinker or corundum, mullite, etc. as refractory aggregates and powders, and admixtures. According to the types of refractory aggregates and powders used, clay-bonded refractory castables are divided into clay, high-aluminum, corundum-mullite, lightweight high-aluminum, etc. It has excellent properties such as good heat resistance and strong anti-stripping. It is mainly used in thermal equipment such as high-temperature furnaces, soaking furnaces, and heating furnaces.
The type and amount of clay binder have an important influence on its performance. The selection of soft clay binder requires good plasticity, strong dispersibility, good bonding, a wide sintering temperature range, and high refractoriness. Its technical requirements are: Al2O329%~35%, Fe2O3<1.8%, R2O<1.1%, ignition loss 10%~14%, and refractoriness greater than 1670℃. The fineness of clay powder is less than 0.088mm, accounting for more than 60%, and its dosage is generally 7%~13%. Production practice has proved that clays such as Guangxi mud, Jiaozuo mud, and ash are better.
Adding dispersants can dissolve and disperse clay colloids and increase the fluidity of castables. Commonly used dispersants include sodium tripolyphosphate, sodium hexametaphosphate, sodium silicate, sodium citrate, sodium tartrate, etc., and their dosage generally accounts for 1%~2% of the clay dosage. Generally, high-aluminum cement or pure calcium aluminate cement is selected as a hardening accelerator, and its dosage is 0.2%~3%. In order to improve the performance of ordinary clay combined castables, the quality of refractory raw materials should be improved, and composite micropowder materials with good dispersibility and composite admixtures should be added. In addition, in order to improve the high-temperature volume stability of the castable, an appropriate amount of kyanite, quartz powder, etc. are sometimes added.
In addition, for clay and high-alumina dense refractory castables with different bonding forms, the standard YB/T5083-1997 has made specific provisions on their grades and classifications. According to the properties of the binder, they are divided into five categories, namely clay-bonded refractory castables, cement-bonded refractory castables, low-cement-bonded refractory castables, phosphate-bonded refractory castables, and water glass-bonded refractory castables.
Special performance refractory castable
A. Alkali-resistant castables
Alkali-resistant refractory castables are alkali-resistant hydraulic castables made of aluminum-silica materials such as refractory clay clinker as aggregate and powder, aluminate cement as binder, and appropriate additives. Standard JC/T708-2013 divides alkaline refractory castables into five types of superior and first-class products according to their performance. Standard JC/T807-2013 divides lightweight alkaline refractory castables into four types of superior and first-class products according to their performance.
B. Acid resistant casting material
Acid-resistant refractory castables are castables made of water glass as a binder, acid-resistant refractory aggregates and powders and admixtures. The raw materials used are mainly cemented clinker, quartz, cast stone, wax stone, etc. Its characteristic is that it still has good performance under the action of medium and low temperatures and acidic media. The corrosion resistance of water glass combined acid-resistant castables is shown in Table 3-143. This type of refractory castable can be used for anti-corrosion chimney linings, acid storage equipment and other equipment linings that are corroded by high-temperature acid gas, etc.
C.Steel fiber reinforced castable
Steel fiber reinforced refractory castables are castables with a certain amount of stainless steel fibers mixed into them, which can improve the strength and toughness of the castables, and have good crack resistance, impact resistance, thermal shock resistance, and wear resistance. Generally, steel fiber is added at 2% to 6% of the castable weight. There are two ways to mix steel fiber castables: one is pre-mixing by the castable manufacturer, and the other is mixing on-site by the user. It is mainly used in kilns such as the building materials industry and the metallurgical industry, where the material is required to have good anti-peeling and impact resistance.
Standard JC/T499-1992 (96) stipulates that steel fiber reinforced refractory castables are divided into four types according to performance: ordinary type and high-strength type.
Insulating Refractory Castables
Insulating refractory castables are made of refractory light aggregate and powder, binder and admixture. General regulations: the bulk density is less than 1800kg/m3, or the total porosity is greater than 45%.
This type of castable has a small bulk density and good thermal insulation performance, also known as lightweight refractory castable. It is widely used. It is generally used as the thermal insulation layer, working layer or load-bearing component on kilns and thermal equipment in industrial sectors such as metallurgy, petrochemicals, electricity and building materials.
There are many varieties of insulating refractory castables, which are generally classified according to the production method of lightweight aggregate varieties, binder types and properties. The most commonly used is to classify according to the lightweight aggregate varieties into lightweight refractory, porous clinker, hollow balls, ceramsite and expanded perlite, vermiculite, etc. The general composition and properties of insulating refractory castables are shown in Table 3-145. The binder is mainly aluminate cement, silicate cement, etc., and its dosage is 15%~40%. Phosphoric acid, aluminum phosphate and water glass are sometimes used as binders. Its admixtures mainly include expansion agents and water reducers. The function of the expansion agent is to offset part of the shrinkage at high temperature and enhance its volume stability.
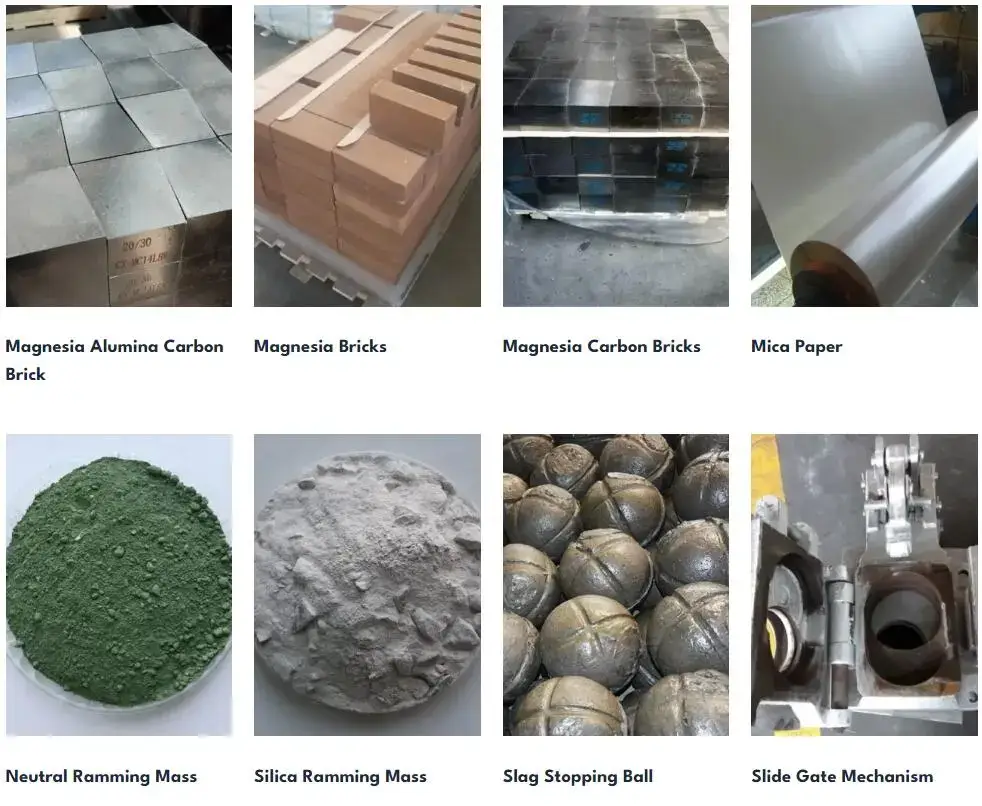
Refractory Products