The stability of continuous casting in the package is to ensure production stability and good quality of cast billet premise. Long life tundish package can reduce the number of times to replace the tundish, which not only reduces the labor intensity of workers, but also can reduce the occurrence of production accidents. Therefore, to improve the age of the tundish has become the production and quality of the pursuit of the direction.
In the actual production process, there are many factors that restrict the age of the tundish, among which the phenomenon of clamping steel in the tundish sizing nozzle occurs from time to time, and has become a common factor that restricts the age of the tundish. Firstly, the clamped steel sizing nozzle cannot be replaced, which reduces the age of the tundish and increases the production cost. Secondly, the seriousness of steel clamping in the sizing nozzle may cause steel drilling accident in the sizing nozzle. Therefore, it is necessary to solve the problem of steel pinching in the tundish sizing nozzle, both from the cost consideration and from the safety point of view.
1.Structure of the sizing nozzle and the condition of the clamping steel
(1) continuous casting in the tundish sizing nozzle outlet is divided into “quick-change” and “pendulum handle type” two kinds.
The “quick-change” mechanism consists of a base, a fixed chute, a spring-loaded movable chute, a lower calibrated spout bracket, and a spring-loaded guard plate. Resistant material part consists of upper nozzle seat brick, upper nozzle, upper sizing nozzle, lower sizing nozzle.
The mechanism of “pendulum handle type” consists of the base of the machine and the reversing fan plate. Resistant material part consists of upper nozzle seat brick, upper nozzle, upper sizing nozzle, lower sizing nozzle and transition block. The working principle and influencing factors of the different structures of the sizing nozzle are also slightly different.
(2) The root cause and state of steel entrapment in the sizing nozzle.
The root cause of the sizing nozzle mouth steel clamping is the gap between the plate is too large, (general sizing nozzle mouth gap requirements ≤ 0.3mm) or sizing nozzle “nest loss” erosion is serious, as shown in Figure 1. From the field sizing nozzle mouth erosion and clamping steel state analysis, sizing nozzle “nest loss” phenomenon is the origin of sizing nozzle erosion clamping steel.
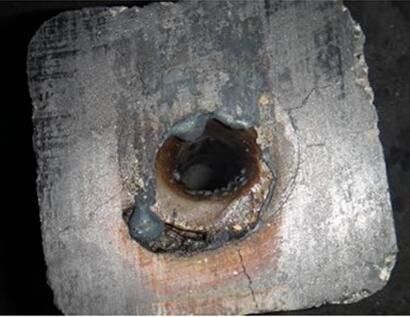
For example: sizing nozzle in the use of the process of up and down in the center of the deviation, artificial control of the flow of casting or on the upper nozzle expansion erosion of serious factors, there will be up and lower sizing nozzle misalignment, exacerbated by the lower wall of nozzle of the erosion of the scouring, the formation of the inner diameter plate between the seam of the phenomenon of “nest loss”. At this time to replace the tundish nozzle operation, will make the sizing nozzle “nest loss” carried within the steel, in the case of sliding or swinging high-speed movement, the steel will be pressed into the sizing nozzle gap, resulting in the phenomenon of sizing nozzle steel clamping.
The general situation produces sizing nozzle folder steel thickness ≤ 1mm, the area size is variable, the largest can be covered with sizing nozzle zirconium core outer diameter edge, as shown in Figure 2. Once the production process is found in the sizing nozzle folder steel phenomenon, we must immediately stop the replacement of the sizing nozzle operation, in order to prevent “through the package” (in the package leakage of steel) the occurrence of accidents.
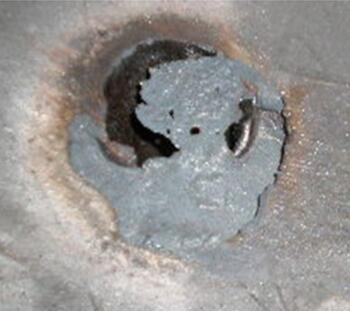
2.Analysis of Influencing Factors and Reasons for Practice
(1)Resistant material factors
Continuous casting of the use of the sizing nozzle is generally aluminum carbon resistant material, internal inlaid zirconium core to increase corrosion resistance, the main component of the zirconium core for ZrO2, adding a small amount of stabilizer (CaO, MgO, etc.) made of.
Sizing nozzle in the process of use, and steel impurity elements (MnO2, SiO2, MgO, Al2O3, etc.) react to generate multiple low melting point oxides, and with the loss of steel, which causes the erosion of the sizing nozzle diameter expansion. In addition, the diameter of sizing nozzle in the burning oxygen diversion or steel cut-off for oxygen burning, will cause serious burns on the diameter of sizing nozzle of the erosion and expansion of the diameter of the diameter of the sizing.
The rationality of the production and design of the sizing nozzle is also an important factor affecting the use of tundish nozzle. Common sizing nozzle process: ingredients → pre-mixing → mixing → molding → drying → sintering → picking → bonding assembly → surface coated with skateboard oil. Strict implementation of the standards of each process to ensure the production of qualified products.
Sizing nozzle size design, generally the upper end of the flared streamlined, in the process of introducing steel into the lower end of the sizing section, its main purpose is to reduce the resistance of steel, reduce steel in the sizing nozzle churning effect, improve the product’s resistance to scouring performance. This reduces the chances of steel pinching in the gap of the sizing nozzle.
The sizing nozzle is a very important factor in the design of the dimensions of the calibrated spout diameter. The empirical formula for the design of the inner diameter D of the sizing nozzle is shown below.
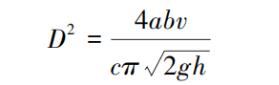
D-Diameter of sizing nozzle outlet of the middle pack, mm;
a,b-Width and thickness of crystallizer cross-section, mm
v-Continuous casting pulling speed, m/min;
c-coefficient, c = λβ.
g-Gravitational acceleration, m/s².
h-Height of the liquid level of steel in the tundish, mm.
In addition to the design of the size of the sizing nozzle, the actual production factors on the impact of the resistant material is also very large, because in the use of the process to withstand the high temperature of the molten steel, the use of the early stage of the spout warming up very quickly, so that the spout of the internal heating is not uniform, and to withstand the molten steel violent thermal shock, which makes the nozzle to produce thermal stress concentration, and the concentration of these thermal stresses is the resistant material to produce the cracks and melting of the source of the loss.
(2)Institutional factors
The “quick-change” mechanism slide, the sizing nozzle bracket and the mechanism base plate must be kept flat. First of all, to ensure that the overall mechanism is not deformed. Secondly, to ensure that the gap between the sizing nozzle to meet the requirements (gap between the sizing nozzle ≤ 0.3mm).
The upper and lower sizing nozzle is mainly dependent on the activities of the slide spring system for compression, so the spring maintenance standards should be high, must ensure that the free height of the same, to ensure that the activities of the slide force balance.
According to the below empirical formula:

Equation:P-the surface pressure provided to the sizing nozzle by the sizing nozzle mechanism.
N-number of surface pressure springs.
μ-spring coefficient of surface pressure spring; ΔX-spring compression during operation
ΔX-the amount of spring compression at work.
If the loaded face pressure spring fails to generate sufficient face pressure, it may result in increased gap in the sizing nozzle and steel pinching. In addition, when replacing the sizing nozzle, the spare sizing nozzle is driven to the use position by the hydraulic cylinder, so the size of the sizing nozzle bracket and the stroke accuracy of the hydraulic cylinder are important control factors to ensure that the upper and lower sizing nozzle are centered to prevent abnormal erosion. Replacement of the entire process of sizing nozzle, if the slide is not flat or uneven force of the movable slide, will make the sizing nozzle to produce a gap, so that the phenomenon of steel clamping.
Pendulum handle type mechanism is through the adjustment of the top wire compression pendulum groove to realize the upper and lower sizing nozzle tightening, in the process of replacing the sizing nozzle oscillating, the fan plate pendulum groove and the mechanism of the bottom plate should be kept parallel to the phenomenon of deformation, to ensure that the pendulum process of sizing nozzle will not produce a gap, so as to avoid the phenomenon of the sizing nozzle clamping steel.
(3)Production process factors
Production process due to the high temperature of steel, steel sleeve eye and other factors, resulting in frequent replacement of the sizing nozzle, which will have a great impact on the life of the sizing nozzle. There is also the effect of steel deoxidation process treatment, the calcium treatment process steel on the sizing nozzle on the existence of a certain degree of melting loss, on this point can only be considered from the sizing nozzle on the material to solve the problem.
In addition to the influence of steel factors, continuous casting replacement of sizing nozzle process also exists human operation problems. For example: in continuous casting in the package open pouring burning oxygen diversion, due to the deviation of human operation caused by the sizing nozzle burned serious, increase the chance of sizing nozzle clip steel. In the process of replacing the sizing nozzle, “quick-change” sizing nozzle slide channel there are foreign objects failed to clean up; “pendulum handle” type sizing nozzle swing process force is not uniform, etc., these are human factors make the sizing nozzle to produce a gap, resulting in the sizing nozzle clamping steel Phenomenon.
3.Measures to prevent steel entrapment in tundish sizing nozzle
(1) Before installing the machine parts, clean up the debris on the base plate of the machine parts, especially the cold steel, and install them after checking that the machine parts and the base plate are free from errors.
Before installing the sizing nozzle, check the board surface is flat without cracks and damage phenomenon, after installing the sizing nozzle, adjust the compression device to ensure that the gap between the sizing nozzle is up to standard (gap between the sizing nozzle ≤ 0.3mm).
Integral mechanism installation is completed, the replacement operation inspection, check whether the replacement process is smooth, accurate measurement of the sliding stroke of the sizing nozzle, to ensure that the upper and lower sizing nozzle port centering.
(2) converter for continuous casting to provide qualified steel, reduce the number of continuous casting to replace the sizing nozzle, improve the continuous casting to replace the sizing nozzle skills, reduce the abnormal erosion of the sizing nozzle caused by man-made operations, the production process should pay special attention to, the slideway and pendulum groove on the foreign matter should be cleaned up.
These are effective measures to avoid the phenomenon of steel pinching in the sizing nozzle outlet during the production process.
In conclusion
(1) Ensure that there is no deformation in the sliding mechanism of the continuous casting sizing nozzle, no foreign matter on the sliding stroke of the sizing nozzle, and that the gap between the sizing nozzle is ≤0.3mm.
(2) The sizing nozzle outlet is reasonably designed, no breakage and crack phenomenon before use, and the plate surface is flat without unevenness.
(3) The rhythm of production is stable, the quality of steel is qualified, and there are no high and low temperatures or steel cut-offs.
(4) Replacement of sizing nozzle personnel skilled, there can be no accidental burning or expansion caused by human factors.
In short, in-depth understanding of the continuous casting in the tundish sizing nozzle of the different institutions of the working principle, and then according to the different factors affecting the determination of the corresponding measures, is able to put an end to the continuous casting in the tundish sizing nozzle of the problem of steel clamping.
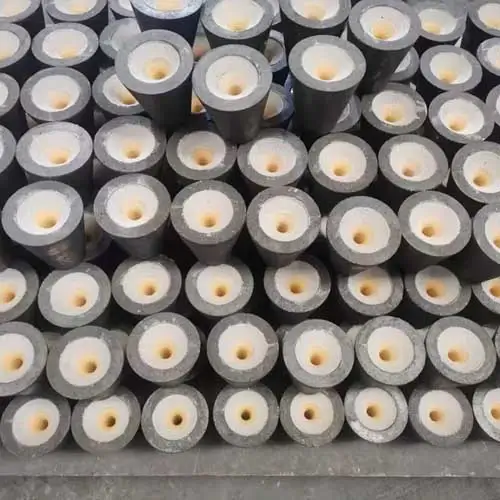