The compactness of the crucible has an extremely important impact on its service life. In order to make the crucible dense and the porosity as low as possible, it is necessary to pay attention to the particle size distribution of the refractory material, so that the gaps between the large-grained refractory materials can be filled with fine-grained materials filling.
In order to let everyone have a more specific impression of the void ratio after knotting granular materials, here is a brief description of the situation of ideal spheres piled up.
(1) General condition of tightness
Spheres of the same size are piled up in a square staggered manner. Each ball is in contact with 6 adjacent balls (4 balls around, 1 ball above and below), and the porosity is 47.64%.
It is easy to obtain the maximum diameter of a small ball that can be accommodated in the gap of a large ball with a diameter of D
(2) Relatively compact situation
(3) The case with the highest compactness
The stacking methods with the highest compactness are square staggered arrangement and tetrahedron-like arrangement.
When uniform spheres are stacked in a square staggered manner, each sphere is in contact with 12 adjacent spheres, 4 spheres around, 4 spheres above and 4 spheres below, and the porosity is 25.95%.
It can be seen from the stacking conditions of several spheres that the porosity is only determined by the arrangement and has nothing to do with the diameter of the spheres. The diameter of the ball is large, and the size of the pores is large and the number is small. The granular refractory materials for furnace lining are all polygonal or even pointed, and their fluidity is very poor. No matter what kind of knotting method is used, the porosity of the most tightly pounded refractory will not be lower than 30%.
In order to reduce the porosity of the furnace lining, the simple and easy measure is to make the particle size in the lining material not so uniform, and the fine-grained material can enter between the closely arranged coarse particles. grain. The requirement of granularity grading comes from this.
Of course, the particle condition of refractory materials is much more complicated than that of an ideal sphere, and the particle size distribution is also extremely irregular. It is impossible to simply calculate the best particle size distribution scheme. The best way is: each foundry will obtain the most suitable grading scheme through experiments based on the actual situation of its own raw materials.
The test method is very simple: mix materials with different particle sizes according to a certain ratio, make them compact under a certain pressure, and then measure their bulk density. When the supply conditions of raw materials change, the particle size distribution plan should also be evaluated through experiments.
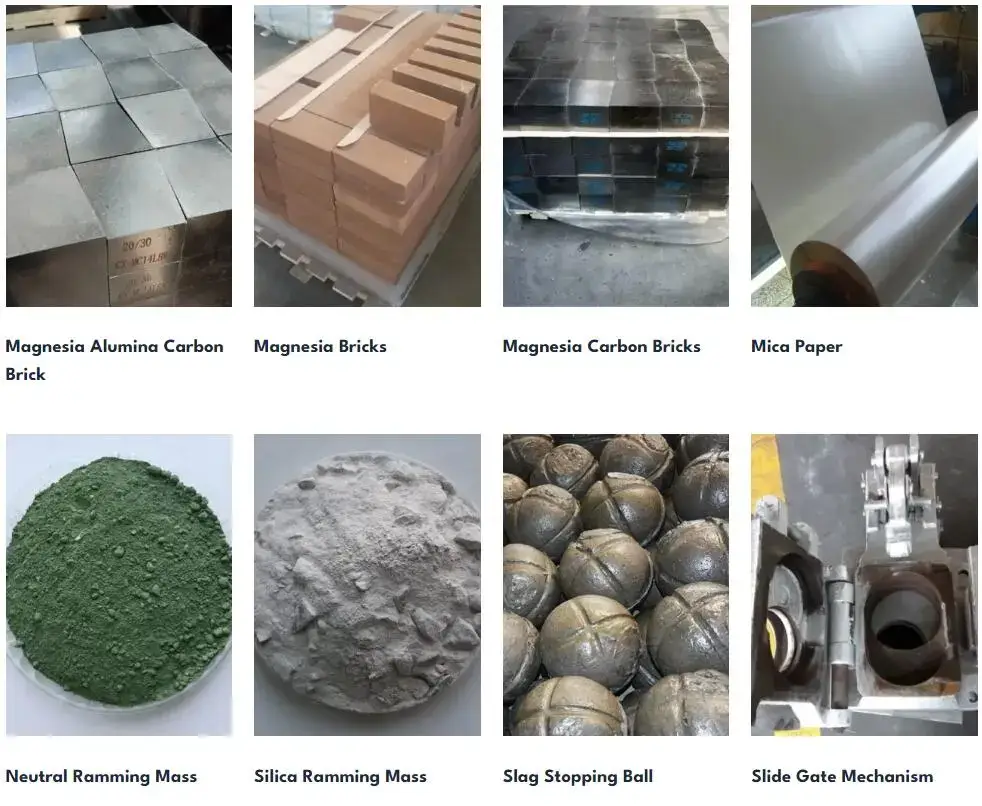