There are many types of unshaped refractory materials, such as refractory castables, refractory plastics, refractory ramming materials, refractory spray coatings, refractory projection materials, refractory mud, etc. Although they are all unshaped refractory materials, they have different material formulas, different particle ratios, different construction methods, different application parts, different target functions, and even more different refractory temperatures.
Refractory castables
Refractory castables are a kind of granular and powdered materials made of refractory materials, which are composed of a certain amount of binder and water. They have high fluidity and are suitable for construction by pouring.
Refractory castables are the main type of amorphous refractory materials. According to the different binders used, their maintenance and molding mechanisms can be divided into three types: hydraulic hardness, gas hardness and fire hardness.
① Hydraulic refractory castables: Castables with cement as binder need water to participate in chemical reactions during the hardening process to form cementitious hardening strength. They are all hydraulic refractory castables.
Cement is the primary factor that determines the strength of castables (especially the strength at room temperature), but its refractoriness is relatively low, so after ensuring the necessary strength at room temperature, the amount of cement should be reduced as much as possible. If it is required for density and ease of construction, refractory powder can be added appropriately. Reducing the amount of cement is also one of the measures to reduce costs.
In construction, it should be strictly avoided to mix aluminate cement with silicate cement, lime, etc. Because these two substances with different chemical compositions will produce hydrated tricalcium aluminate after mixing, which greatly reduces the strength.
② Air-hardening refractory castable: refers to the binder that absorbs CO2 in the air during maintenance and gradually solidifies and hardens. The most commonly used refractory castable is water glass refractory concrete.
In addition to high temperature resistance, water glass refractory castable also has acid resistance and wear resistance, so it is often used as the lining of chemical equipment.
The hardening process of water glass refractory castable under natural conditions is very slow, and a coagulant (sodium fluorosilicate, high alumina cement, etc.) needs to be added during construction.
③ Fire-hardening refractory castables: Castables with phosphoric acid and phosphate as binders need to be heated and baked to obtain strength and high-temperature performance, so they are called fire-hardening refractory castables.
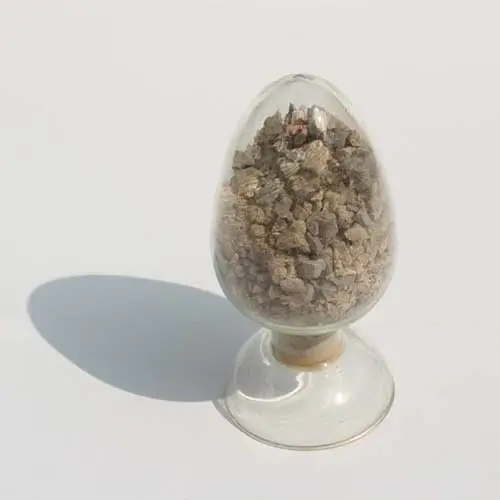
Refractory plastics
Plastics are made of powdered and powdered materials combined with binders and plasticizers such as plastic clay, adding a small amount of water, and fully mixed to form a kind of amorphous refractory material that is in a paste state and maintains high plasticity for a long time.
Granular and powdered materials are the main components of plastics, generally accounting for 70% to 85% of the total. It can be composed of refractory materials of various raw materials, and plastics are often classified and named according to the raw materials. Because this amorphous refractory material is mainly used in various heating furnaces that are not directly in contact with the molten material, clay clinker and high-aluminum clinker are generally used. Lightweight granular materials can be used to make lightweight plastics.
Plastic clay is the primary component of plastics. Although it accounts for 10% to 25% of the total plastics, it has a great influence on the plasticity of plastics, the bonding strength between plastics and their hardened bodies, volume stability and fire resistance. In a certain sense, it can be considered that the properties and quantity of clay control the properties of plastics.
Generally, plastics are required to have high plasticity, and after long-term storage, they still have a certain plasticity, which is called the workability of plastics. Plasticity is related to the characteristics of clay and the amount of clay used. In addition, it mainly depends on the amount of water, which increases with the addition of water. However, too much water will bring adverse effects. Generally, 5% to 10% is appropriate. In order to prevent the plasticity of plastics from decreasing significantly during its shelf life, hydraulic binders cannot be used.
Plastics do not require special skills during construction. When used to make furnace linings, take the plastic out of the sealed container, spread it between hanging bricks or hooks, and tamp it with a wooden hammer or air hammer (each layer is 50mm to 70mm thick). Before hardening, surface processing can be performed. In order to facilitate the discharge of moisture, air holes are opened at certain intervals. Finally, expansion and contraction joints are set according to the design. If used to make the entire furnace cover, it can be constructed on the bottom mold first, and then hoisted after drying.
The application temperature of plastic base mainly depends on the quality of granular and powdered materials used. For example, ordinary clay can be used below 1300℃~1400℃, high-quality ones can be used at 1400℃~1500℃; high-aluminum ones can be used at 1600℃~1700℃ or even higher; chromium ones can be used at 1500℃~1600℃.
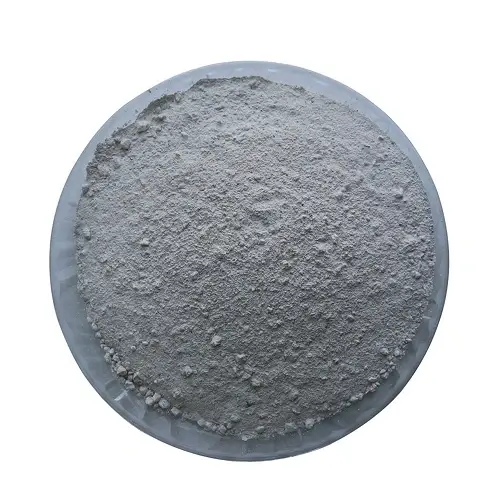