Crucible furnace lining is a key component of medium frequency furnace, crucible furnace lining can be divided into three categories of acidic furnace lining, alkaline furnace lining and neutral furnace lining according to the composition, and the use of which kind of furnace lining should be fully considered the production process and the composition of steel.
The neutral furnace lining of Al-Mg-Al-rich spinel crucible is mainly used in steel mills for smelting high speed tool steel, die steel, stainless steel and other high-end special steels with extremely strict composition requirements. The physical properties of Al-Mg-Al-rich spinel crucible, such as the coefficient of linear expansion and thermal shock resistance, etc., are better than those of the other furnace lining, which can meet the strict requirements of the composition of the molten steel as well as slag indexes of the River Metallurgy Science and Technology Corporation (HMST).
How to improve the service life of the neutral lining of large medium frequency furnaces has always been a practical problem that the industry urgently needs to solve. By understanding the causes of defects in the lining and avoiding them in time during the production process, the lining can be effectively prevented from deteriorating sharply. This is also one of the main research directions for improving the service life of the lining for various companies. The initial knotting thickness of the lining of Heye Technology is 130mm, and the offline thickness is 50mm. Through 3a of exploration, the system has been comprehensively improved and optimized from the lining material ratio, steel mold, knotting process, sintering, and smelting. The maximum furnace age has been increased from 22 furnaces to 33 furnaces, and the furnace age has increased by 50%. At present, there is little research on neutral linings. The most common defects of linings are four types: overall enlargement of the middle part (commonly known as “big belly”), local enlargement of the middle part, peeling, and cracks.
Overall enlargement of the center
1 Reason
Neutral furnace lining through high-temperature sintering to form a crucible rich in aluminum-magnesium spinel network, the theory of aluminum-magnesium spinel and alumina furnace lining melting point similar to 2050 ℃, but consider its refractoriness in 1750 ℃, temperature measurement point and the furnace in the middle of the existence of temperature difference and other factors, the general steel smelting temperature control in the steel below 1650 ℃, due to the process requirements of strict requirements resulting in a long period of time for smelting the part of the mill needs to request the process of the steel temperature ≤ 1600℃. In short, the longer the smelting time, the higher the temperature, the lower the service life of the furnace lining. Steel in the role of electromagnetic force in the middle of the furnace lining to form a whole circle of steel collision zone, sharply accelerating the region of the furnace lining erosion rate.
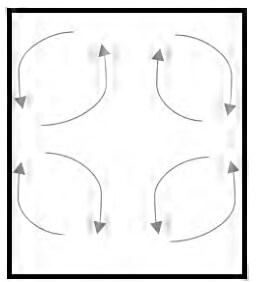
The main reason for high temperature erosion is “bridging”, which can be generally divided into two situations.
1) Poor slag fluidity. The main reasons are that the incoming charge carries impurities, the process requirements of reducing silicon and manganese, and the addition of iron oxide scale and other slag regulators such as quartz sand and fluorite are not suitable in terms of quantity and timing;
2) Improper charge shape or charging sequence causes the charges to squeeze each other and form “bridging”.
2 Measures
Into the furnace material impurities and process requirements of the slagging agent can be adjusted, due to the different circumstances of each company, we do not discuss here, fluorite as a “double-edged sword”, as the furnace lining smelting “marijuana”, with less slag mobility is poor, more erosion of the furnace lining, so the degree is very difficult to control, but between different steel grades can be figured out through the actual production of a range of amounts added, and then the minimum value of the initial amount of fluorite added to the induction loop below the 400mm position. This degree is very difficult to control, but between different steel can be groped through the actual production of a joining amount range, and then the minimum value for the initial amount of fluorspar to join the steel to reach the induction ring below the upper edge of the 400mm position to join (different tonnage of different heights of the furnace lining, the purpose is to avoid the daily erosion of the most serious parts), and at the same time to add slag adjusting agent, the steel to reach the position of the upper edge of the induction ring according to slag mobility can be made up for the addition of fluorspar. The slag can be added after the steel reaches the upper edge of the induction ring. Furnace material bridging itself is less, because as long as the material is not in the induction loop outside the upper edge of the position, can be melted, so as long as the large pieces of material lifting into the furnace, it can be effectively avoided.
Localized enlargement in the middle
2.1 Chemical erosion
2.1.1 Causes
The alkalinity of the slag should be compatible with the furnace lining material, neutral furnace lining to acidic oxides or alkaline oxides have a certain degree of corrosion resistance, so for the
In chemical erosion should pay extra attention to CaF2 erosion, especially when smelting high-carbon steel, molten steel mobility is good, which exacerbates the chemical erosion.
2.2 Mechanical damage
2.2.1 Causes
When the sharp end of the large block of material into the furnace, the impact of the furnace lining to cause localized damage, the location of the damage to form a weak point, in the same high temperature as well as other erosion, it is more likely to appear damage. At the same time, the formation of localized enlargement of the furnace lining, the most obvious feature of this situation is that the defect location in the pouring position directly opposite.
2.2.2 Measures
1) Reasonable batching. The best way for the crumbs and blocks to join the way of alternating, can effectively avoid mechanical damage;
(2) For 20t medium frequency furnace, the single weight of more than 300kg of material required to be hoisted into the furnace, do not use the charging truck to join.
Flaking
3.1 The moisture content of the furnace lining is too high
3.1.1 Reasons
At 100℃ and a standard atmospheric pressure, the volume of water expands 1618 times after it changes from liquid to water vapor. If the moisture content of the furnace lining material is too high or damp, and the backing bricks and coil slurry are newly replaced and not completely baked to drain the moisture, when the furnace lining is knotted and sintered, the rapid temperature rise will cause the large amount of water vapor generated rapidly inside the furnace lining to be unable to be quickly discharged from the exhaust hole of the crucible mold and increase the pressure, and finally break through the surface of the furnace lining sintering layer, causing the surface of the furnace lining sintering layer to be pushed out and peeled off. This situation usually occurs in the first three furnaces of the furnace lining, and it can be seen in the first furnace.
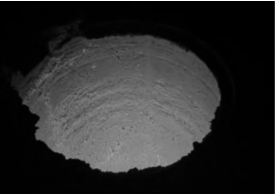
3.1.2 measures
For moisture, knotted furnace lining before the new repair coil cement, and replacement of the backing brick, can be set up in the furnace crucible mold after electric heating with an electric furnace after high-temperature baking, thoroughly exhaust the crystalline water and water vapor in which the leakage current to maintain the value of more than 4h in normal production as a standard; after the purchase of furnace lining materials should be used early and moisture-proof measures to prevent the lining of the furnace back to the moisture; build the furnace should be a coil before the test water test pressure to Prevent the internal circulating water micro-leakage, resulting in moisture into the furnace lining, in the sintering operation, the temperature should be slow, and the crucible mold should have venting holes, to ensure the normal overflow of moisture.
3.2 Expansion coefficient is different
3.2.1 Reason
This phenomenon often occurs in the hot surface of the furnace lining is infiltrated by iron and non-infiltration of the combined parts. Infiltrated hot lining and non-infiltrated cold lining interface in the hot and cold cycle changes, due to the different expansion coefficients and produce interface separation. The second is that the furnace lining later due to the thickness of the lining after erosion is different, the location of the lining thicker will also be due to the different coefficients of expansion to produce spalling.
3.2.2 Measures
Steel through the middle or easy to erode parts, as soon as possible to let the steel rise through, to avoid this stage of the melting of large pieces of material, furnace lining thick position spalling frequency is low and has no effect on the overall use of the furnace lining, can not do special treatment.
3.3 Uneven knotted density
3.3.1 Causes
Knotting quality of the lining directly affects the service life. Knotting quality of the lining is related to the sintering quality, sintering quality affects the use of performance.
(1) When knotting the furnace lining material particle size is not uniform, coarse and fine particles produce segregation, the furnace lining knotting vibration is not solid, which will lead to the lining is not dense or local loose, when the liquid metal pressure is high, it may produce spalling or leakage;
(2) the roundness of the furnace lining steel mold does not meet the requirements, will lead to gas vibration wall vibrator in the vibration process part of the position can not be knocked to, resulting in not knocked to the part of the lining density is not enough;
(3) unstable gas source of gas wall vibrator will lead to different positions in the process of density deviation, resulting in uneven density.
3.3.2 Measures
(1) When knotted furnace lining, use a single packet of 25kg quality of small packets of furnace lining material, in addition to moisture-proof, in the process of transportation of the lining can also effectively avoid the vibration generated by the segregation;
(2) The roundness of the furnace lining steel mold must be guaranteed, the general requirements of the mold inner diameter of the different positions of the deviation is not greater than ± 1mm;
(3) gas vibration wall of the general use of compressed air, compressed air supply must be temperature, it is best to use a separate gas station or air compressor gas supply;
(4) by increasing the gas pressure can also be effective in improving the densification of the furnace lining, thereby improving the age of the furnace, but improve the gas pressure must be considered to increase the maximum bearing pressure of the gas hammer, the thickness of the steel mold bearing pressure and vibration conduction force and other influencing factors.
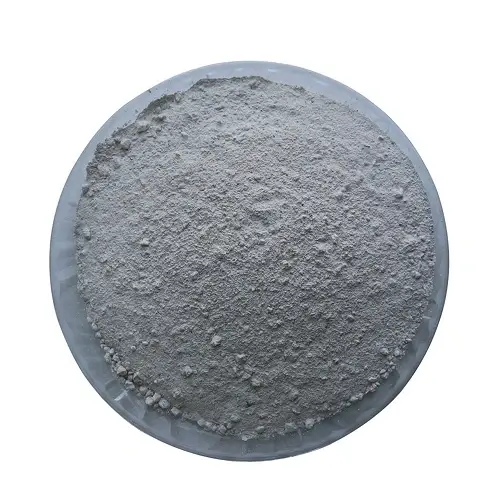
Crackles
4.1 Slagging
4.1.1 Causes
Since the slag and furnace charge bring in a large amount of oxides such as SiO2 and Al2O3, these oxides flip up and down with the electromagnetic stirring. When they touch the furnace wall, they will adhere to the surface and form slagging on the furnace wall. In addition to causing a decrease in input power, due to the different thermal contraction ratios between the furnace lining and the slag hanging on the furnace wall, it will also cause tensile cracks. This type of crack generally appears in the middle and upper part of the furnace lining, mostly at the slag line.
4.1.2 Measures
By controlling the aluminum content of the charge with the furnace, to avoid the oxidation of aluminum elements in the molten steel to form Al2O3 oxides; to avoid the upper furnace with residual slag; to replace the single aluminum deoxidation by a variety of deoxidation methods.
4.2 Intermittent production
4.2.1 Reason
Medium frequency furnace because each furnace will be poured steel, continuous production is actually a short-term low-temperature – high temperature – low temperature cycle of rapid cooling and heating, but the thermal shock of the neutral furnace lining is the best of all types of furnace lining, so this production mode has less impact on it. In the actual production process due to internal or external reasons, most of the medium frequency furnace will be based on the production of intermittent production mode, which will cause the low temperature / high temperature temperature difference is very large, so it is very easy to produce cracks. Cracks are divided into two categories: transverse cracks and vertical cracks. Vertical cracks will gradually heal through their own expansion during the use of the furnace lining, while transverse cracks are difficult to heal by themselves due to the lack of sufficient pressure at the mouth of the furnace.
4.2.2 Measures
(1) Different cold furnace start-up processes should be set according to different furnace stopping times;
(2) after the steel such as the need to stop the furnace, a short period of time to stop the furnace can be poured into the furnace for insulation, such as stopping the furnace time > 2h, it is necessary to use insulation materials to cover the mouth of the furnace, the gaps are closed using rock wool and other insulation operations, can effectively guarantee that the entire lining of the furnace is in the process of relatively uniform temperature reduction.
4.3 lining knotted charging layer and layer combination is not dense
4.3.1 reason
In the lining of the furnace lining knotted before adding material, the lining material layer and layer combination is not tight, it will cause the knotted lining of the furnace lining density is low, the sintered sintered layer after sintering strength is low. Furnace wall crack tendency is greater. The main reason is that the thickness of the single layer of the furnace lining is greater than the length of the exhaust fork tines, resulting in the use of exhaust fork sand process, can not be two layers of the intersection of the location of the stir or hand-tying after a layer of hand-tying, not the surface of the loose raking on the addition of material will lead to delamination.
4.3.2 Measures
(1) the length of the exhaust fork tines must be greater than the thickness of a single layer of furnace lining material 1.5 times, to ensure that the fork sand process will be two layers of the intersection of the location of the churning and lining material in the pouring process to ensure that the thickness of a single layer of different locations of the thickness of the uniformity of the general in the mouth of the whole circle of the furnace evenly fixed dumping position;
(2) If you use a manual vibrator for knotting, each knot must be a layer of the surface for picking loose, so that the layer and the layer produced between the intersection, I plant the use of pneumatic vibration of the wall, by knocking the furnace lining mold when the lining of the furnace lining knotted solid.
Conclusion
1) “Bridging” causes the greatest loss to the furnace lining. By controlling the timing and amount of fluorite addition, the fluidity of the slag can be effectively adjusted and chemical erosion can be avoided to the maximum extent. At the same time, the slag permeability can be improved through a reasonable slag adjustment process, and the “bridging” phenomenon can be avoided.
2) Mechanical damage to the furnace lining can be effectively avoided by optimizing the order and method of adding the charge into the furnace.
3) The water vapor content of the furnace lining is tested before entering the site, and moisture-proof measures are taken. If it does not meet the standards, it shall not be used. The furnace is dried strictly according to the process to ensure that the water vapor is effectively discharged. During the smelting process, it is necessary to avoid the molten steel staying in the most severely eroded part of the furnace lining for a long time to avoid peeling.
4) The temperature difference is fatal to the furnace lining. It is very easy to have various cracks, especially transverse cracks, which cannot be healed naturally. Therefore, during the cooling process, it is necessary to try to ensure that the temperature drop of the entire furnace wall is relatively uniform to avoid crack damage.
The use process of the medium frequency induction furnace is a complex system issue. The key lies in the maintenance of the use process. Only through strict operating procedures, scientific smelting systems and careful maintenance by personnel can the ultimate goal of increasing furnace life, reducing costs and increasing efficiency be achieved.