Indefinite refractory material is a kind of refractory material that can be used directly without firing, which has the advantages of fast construction, simplified process, energy saving, good integrity, easy to replace, etc., and is widely used in metallurgical field. Among them, pummeling material is a kind of indefinite refractory material which is constructed by pummeling (manually or mechanically), formulated by a high proportion of granular material and a low proportion of binding agent and other components, and hardened under the effect of heating higher than room temperature. The use of magnesium tamping material in the copper water jacket of the flue gas outlet of the electric furnace roof and oxygen-rich side-blowing furnace not only meets the process requirements, but also reduces the production cost.
Magnesium ramming mass is made of fused magnesia as raw material, with binder, anti-cracking agent, stabilizer and other materials added, and stirred into dry mixture. Magnesium ramming mass has good chemical properties, is resistant to erosion, wear, spalling and thermal shock, and is widely used in metallurgy, building materials, non-ferrous metal smelting, chemical industry, machinery and other manufacturing industries.
1、Drying and maintenance of magnesium pounding material before use
In the drying process before the use of amorphous refractories, the surface moisture is first evaporated by heat, and the heat is transmitted from the surface to the interior, so that the temperature of the adjacent parts gradually increases. Due to the evaporation of surface moisture, the moisture (vapor) inside the refractory material gradually diffuses to the surface to replenish. If the heat supply is too large, the temperature rises too quickly, then the amount of steam produced per unit of time is too much, due to the poor permeability of indeterminate refractories, the internal moisture (steam) to the external diffusion of obstruction. At the same time, due to the vaporization of water, the volume increases dramatically, the refractory material will produce a large internal tension, if the tension exceeds the compressive strength of the refractory material, will lead to refractory expansion crack; the difference between the two will be spalling or cracking. Therefore, the conventional heating and drying requirements are high, and can not guarantee the performance of refractory materials. The magnesium pounding material can be dried naturally at room temperature, avoiding the damage of high temperature to the refractory material and effectively guaranteeing the performance of refractory material.
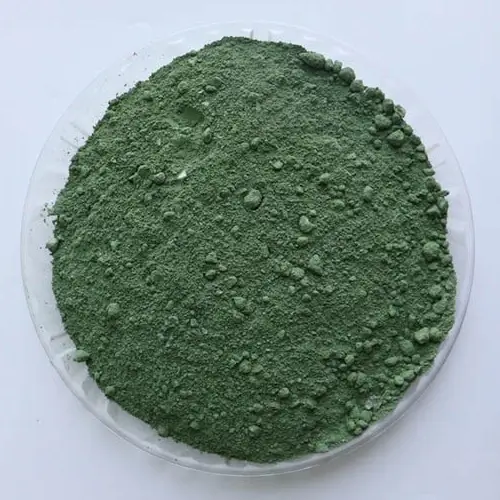
2、Magnesium pounding material high temperature use principle
The magnesium pounding material used is made of magnesium sand (aggregate) and magnesium powder (powder) modulated in a certain proportion and through a certain density of a certain binding agent, the main component of which is MgO, and its thermal properties are as follows: melting point of 2825 ℃, thermal conductivity of 45W/(m-K), coefficient of thermal expansion of 14×10-6-℃, heat capacity of 53.6J/mol at 1500K, and good thermal shock resistance.
Under high temperature use conditions, MgO has good anti-temperature performance. At the same time, the magnesium batter contains a small amount of CaO and Fe2O3.Under the production conditions, CaO and Fe2O3 in the batter react to form dicalcium ferrate (C2F) with the reaction formula:
2CaO+Fe2O3=2CaO-Fe2O3 (1)
(1)The melting point of dicalcium ferrate is 1449℃, but in the presence of ferrofluid (produced by the decomposition of high-valent iron at high temperatures), the temperature at which the liquid phase appears is only about 1100℃. And magnesium pounding material usually contains a small amount of SiO2 and Al2O3, the temperature of the liquid phase is lower than 1100 ℃. In the production conditions (such as electric furnace operation), the tamping material from 1100 ℃ local liquid phase, the material began to sinter, with the rise of furnace temperature, the amount of liquid gradually increased, the material working surface continuously sintered and solidified, the formation of a dense sintered layer.
(2) The C2F in the liquid phase, under high temperature conditions, undergoes a phase transition to form a new phase with high melting point, which improves the stability of the material at high temperature.
(3) MgO, the main component in magnesium pounding material, is transformed into stable cubic crystals (magnesite) under high-temperature heating conditions, and it can be seen from the CaO-FeO-MgO phase diagram that, when the FeO liquid formed after the decomposition of C2F comes into contact with a large amount of magnesite, FeO will be gradually absorbed by the magnesite to form solid solution [(Mg-Fe)O magnesium fuchsite], and the melting point will gradually increase with homogenization . CaO, on the other hand, reacts with SiO2 within the material or in the slag to produce silicate phases such as C2S and C3S with relatively high melting points, which improves the stability of the material at high temperatures and its resistance to erosion and scouring.
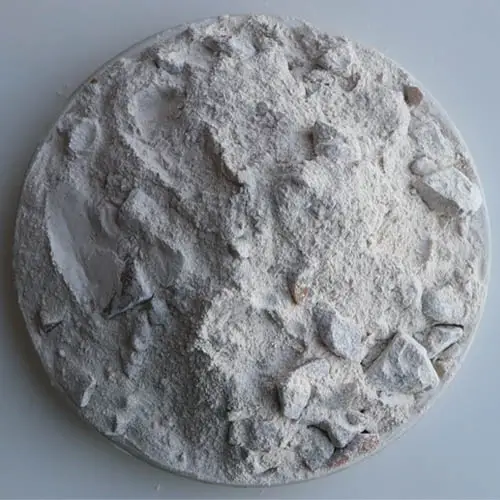