High-aluminum refractory materials have high stability against blast furnace slag, molten iron erosion, and wear at high temperatures, and are inert to carbon monoxide. However, in alkaline media, when working under high temperature conditions, it is found that corundum is converted into β-alumina. This conversion is accompanied by a 20% increase in volume, which leads to fragmentation. The matrix first interacts with alkali vapor. Corundum bricks use mullite or chromium-aluminum matrix instead of corundum to improve the stability of the product against alkali.
Further improvement of the efficiency of blast furnace refractories is the use of silicon carbide products; especially for the lower part of the furnace and the lining of the furnace belly. Silicon carbide – chemically inert, wear-resistant, silicon carbide refractories have very high stability, and are more stable to oxidation than carbonaceous products. The main problem in the application of silicon carbide products in blast furnaces is to develop a binder with sufficiently high stability to alkalis. From the experiments, tar-bonded silicon carbide graphite products, ceramic (clay)-bonded, oxynitride and nitride-bonded silicon carbide products, nitride Si₃N4 and oxynitride Si₃ON₂ bonded products have better stability. However, self-bonded silicon carbide products were found to be more alkali-resistant. Since self-bonded silicon carbide products are difficult to manufacture, refractories with various combinations of silicon carbide content are studied: high-aluminum silicon carbide, graphite silicon carbide, etc.
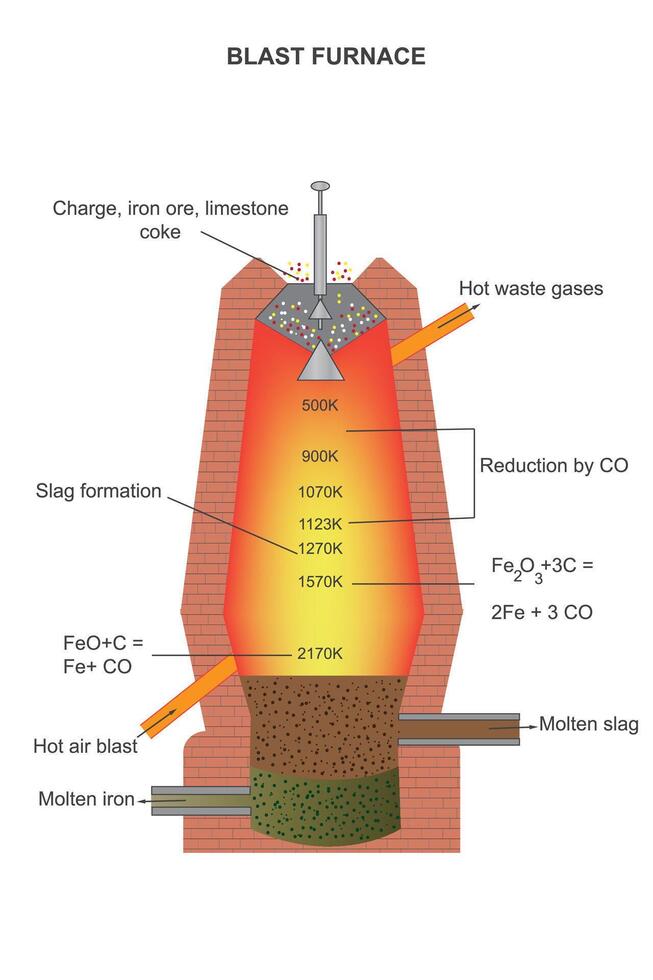
Magnesium refractory materials have been tested in the lower part of the furnace body, the waist and the belly. Its life index is higher than that of high-quality clay bricks, but lower than that of silicon carbide. The selection of suitable refractory materials for the lower part of the furnace body and the belly is still ongoing.
The lower part of the furnace body and the belly have been in continuous operation for 5 to 8 years, and in some cases for 10 to 12 years. The intermediate repair of the furnace body and the belly (level II overhaul) ① usually takes 12 to 18 days to complete. It is to stop the furnace, blow off the lining, cool, inspect, replace the lining, overhaul metal components and equipment and the furnace. Repairs in some occasions are mainly carried out by gunning. It is composed of the same raw materials used in the production of dense bricks, and uses alumina cement or high-alumina cement with low iron oxide content as a binder. It is known that it is a method of not stopping the furnace and repairing the volume is not large. In this case, the refractory mud of special composition passes through the hole of the furnace shell and is completed in the furnace at a pressure of less than 1.5MPa. This type of mud uses a binder or high-alumina cement combined with coal tar with a softening temperature exceeding 200°C, diluted liquid oil, asphalt or water glass.
① Grading of blast furnace lining maintenance: Level I: maintenance of furnace body and hearth; Level II: maintenance of furnace body; Level III: maintenance of furnace throat.
Repair of the upper part of the furnace body (level II repair) can be sprayed without cooling the furnace.
The furnace bed and the furnace lining are basically made of carbon bricks. The superiority of carbon products is that it has high refractoriness (over 3000℃) in reducing or inert atmosphere, increases strength with increasing temperature, maintains constant volume in a wide temperature range, has good thermal shock resistance, is non-wettable to metals and slags, and can produce large bricks with strict tolerances. The furnace bed is laid with 3~4 rows of large carbon bricks with wrinkles, up to 1.5~3.5m long, with a cross-sectional area of (0.5~0.65)m×(0.5~0.65)m. The wall above the furnace bed is laid with large carbon bricks. The upper series of the center of the furnace bed is completed with high-aluminum wrinkled (preventing floating) bricks. In order to prevent bricks from floating, the so-called top laying method is also used for brick laying. The minimum temperature for the interaction between refractory materials and pig iron is 1100~1150℃. If high-aluminum products are used on the upper part of the furnace bed, the 1100~1150℃ isotherm will pass along the surface of the brick, causing the iron-out temperature to be around 1450℃. When the 1100~1150℃ isotherm layer of high-aluminum bricks becomes thinner, the temperature of the outer layer of the bricks increases and the iron-out temperature decreases.
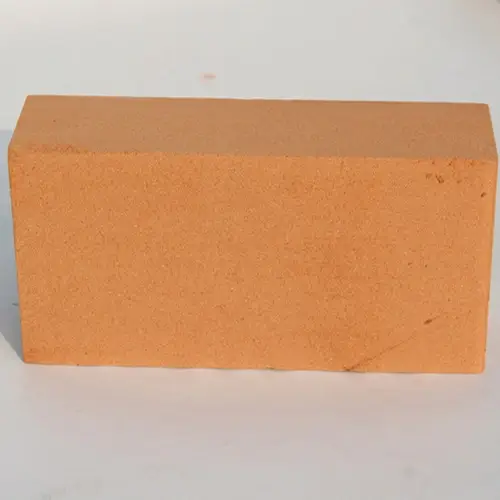
Thus, the tapping temperature becomes an indicator of the state of the furnace bed lining. Larger furnaces are equipped with regulated cooling from below the hearth. The main cause of hearth damage (brick floating) is the penetration of iron into the serrated joints between bricks under the action of the static pressure of iron. Therefore, the hearth masonry is pre-assembled on a carefully prepared large brick test bench. The total thickness of the refractory masonry of the hearth of larger furnaces reaches 5 m. It is necessary to prevent accidental iron cracks in the furnace base due to heating (especially uneven) and hearth damage.
The hearth is built with carbon and aluminum silicate refractory masonry. The carbon masonry of the hearth walls is cooled with the help of standard cooling devices or water jackets (two-layer furnace shell). The upper part of the hearth (tuyere zone) is suitable for masonry of silicon carbide refractory.
Historically, effective refractory materials have been selected. It is believed that the carbon released during the decomposition of carbon oxides is stored in the pores and cracks of refractory products, which leads to refractory damage. Magnesium oxide and deposited zinc in the composition of refractory materials are considered to be catalysts for this reaction. In order to reduce the carbon increase of steel, dense products with minimum iron oxide content are used. However, it is more important to increase the life of the blast furnace lining.
Later, attention was directed to the destructive effects of alkali vapors. The alkali content of the blast furnace charge reaches 10% to 15% in the lower part of the furnace body in contact with the lining (peripheral area), while the central part of the furnace contains 1% to 2%. The interaction between the refractory lining and the alkali includes the following stages: the formation of vapor containing alkali compounds, penetration into the interior of the refractory, condensation, melting, filling of pores, and reaction of the melt with the furnace gas medium. When SiO2 is present in the refractory (in mullite particles or in the matrix), alkali compounds are formed: K2O·Al2O3·4SiO2 leucite, K2O·Al2O3·2SiO2 nepheline, Na2O·Al2O3·2SiO2 nepheline, K2O·6Al2O3 and Na2O·6Al2O3·β-alumina, Na2O·Fe2O3·4SiO2 nepheline; K2O·Al2O3·6SiO2 orthoclase. The formation of alkali-containing aluminum silicates, with a volume increase of up to 45%, causes stress generation and the formation of new fractures. The open porosity of the aluminum silicate refractory saturated with alkali is reduced to 2.5%. Mullite is dissolved under the action of alkali, and the alkali compounds may be reduced and decomposed under the action of carbon. At 1500°C, gaseous potassium and metallic silicon are formed. Cyanides KCN and NaCN are formed in the lower part of the furnace. Part of the cyanide leaves rapidly with the gas, while the rest reacts with the refractory to form a melt.
The study of the interaction between alkali and refractory materials has undoubtedly proved that refractory materials containing SiO2 cannot be accepted in the lower part of the blast furnace structure.
It is known that corundum products (Al2O3 95%~98%) are stable to alkali. However, this is not the most appropriate judgment. Corundum products have shown the formation of β-alumina, and in addition have a high linear expansion coefficient, which makes it crack.
The refractory material itself interacts with iron, and even all of them have thermodynamically possible reactions. Under the action of iron, the refractory material is only slightly damaged because the interaction speed is not high, and the reaction products form a hard inert protective layer. At 1500℃, the wetting angle of iron to most refractories is greater than 100°.
In recent years, carbon, especially silicon carbide refractories, have been successfully used in blast furnace linings. Silicon carbide refractories have the following advantages over other blast furnace refractories: high stability to alkalis, good thermal shock resistance and high thermal conductivity, and the smallest pore size. In this way, silicon carbide products squeeze out all other refractories from the lower structure of the blast furnace. Silicon carbide refractories combined with graphite are considered promising.
The later developed Sialon combined with silicon carbide products have larger crystals, lower porosity, and better oxidation resistance than those combined with silicon nitride, and are tried in the middle section of blast furnaces in some countries.
The chemical mineral composition of blast furnace refractory materials puts forward requirements for it according to the porosity. It is believed that the porosity of the product is less than 12%, which significantly reduces its slag infiltration, but the infiltration does not have a brake property. The wear of products with a porosity of less than 12% at room temperature is 5~6 times lower than that of products with a porosity of 17%, and 10~20 times lower at 980℃.
Cooling is an important factor in the stability of the blast furnace lining.
The hearth and hearth linings are used continuously for 15 to 20 years. During this period, the blast tuyere, iron and slag outlets are overhauled according to the comprehensive process. The tuyere is made of special quality refractory materials and replaced according to the wear. When the iron and slag are discharged in each cycle, special taphole mud is driven into the iron outlet. The taphole mud should have plasticity and stability to molten iron and slag liquid, high hardening speed, and it should not secrete smoke or harmful gases that pollute the environment.
Tar-bonded anhydrous taphole mud is now widely used, which contains silicon oxide, high-aluminum materials, silicon carbide, a small amount of carbon and clay, and about 15% coal tar or asphalt. However, this mud hardens slowly, forms smoke, and creates cumbersome working conditions. Using tar of phenol formaldehyde as a binder can eliminate the disadvantages. It is thermally reactive, that is, it turns into a solid state when heated. The solvent of tar uses ethanol, and the Al2O3-SiC-C system and MgO-C system mud have high stability to the tar of phenol formaldehyde. With this mud, the repair time of the iron outlet is shortened, which is conducive to increasing the output of the furnace.
The refractory material of the blast furnace iron outlet groove should have high chemical stability, wear resistance and stability to temperature changes when the temperature is increased. To increase the life of the groove lining, adopt: high aluminum material with silicon carbide; silicon carbide, silicon carbide alumina and silicon nitride combined silicon carbide. Silicon carbide mud combined with silicon nitride has a relatively good life. The characteristics of silicon nitride are: high strength with low thermal expansion and maximum thermal conductivity at the operating temperature. Therefore, this binder has high thermal shock resistance. In addition, when the temperature is increased, an oxide film is formed on the surface of the silicon nitride crystal to prevent the wear of the binder.
The life of the iron outlet groove lining depends not only on the properties of the refractory material, but also on the furnace working system, the method of realizing the lining and the structure of the groove itself. The iron trough of my country’s large blast furnaces has developed from ramming materials to castable materials, which are mainly made of fused corundum, silicon carbide, a small amount of metal silicon and metal aluminum powder, appropriate amount of coagulant, debonder, ultrafine powder and other high-grade raw materials. Castable materials are used in some blast furnaces and have achieved good results.